Die Zukunft des Schulbaus steht neben dem Parkplatz von Werk 2 des Modulbau-Unternehmens Kleusberg im ostdeutschen Kabelsketal, nahe der Stadt Halle/Saale. Das Mustergebäude ist ein riegelförmiger, eingeschossiger Quader mit Flachdach und Holzfassade. Er stammt aus dem Schulbaukasten des Unternehmens, der dank vordefinierter Module kürzere Bauzeiten bei gleichzeitig hoher architektonischer Flexibilität ermöglicht. Die Einheit besteht aus modernem Klassenzimmer, Nebenräumen und Sanitärbereich. Neben der verkürzten Bauzeit punkten die neuen Schulen auch im Bereich Nachhaltigkeit: Sie lassen sich bei Bedarf an einem anderen Ort neu errichten und am Ende ihrer Lebensdauer zu fast 100 Prozent recyceln. Kleusberg und die Managementberatung Porsche Consulting zeigen hier ein gemeinsam entwickeltes bedarfsgerechtes und nachhaltiges Konzept. Klassische Probleme am Bau scheinen damit lösbar.
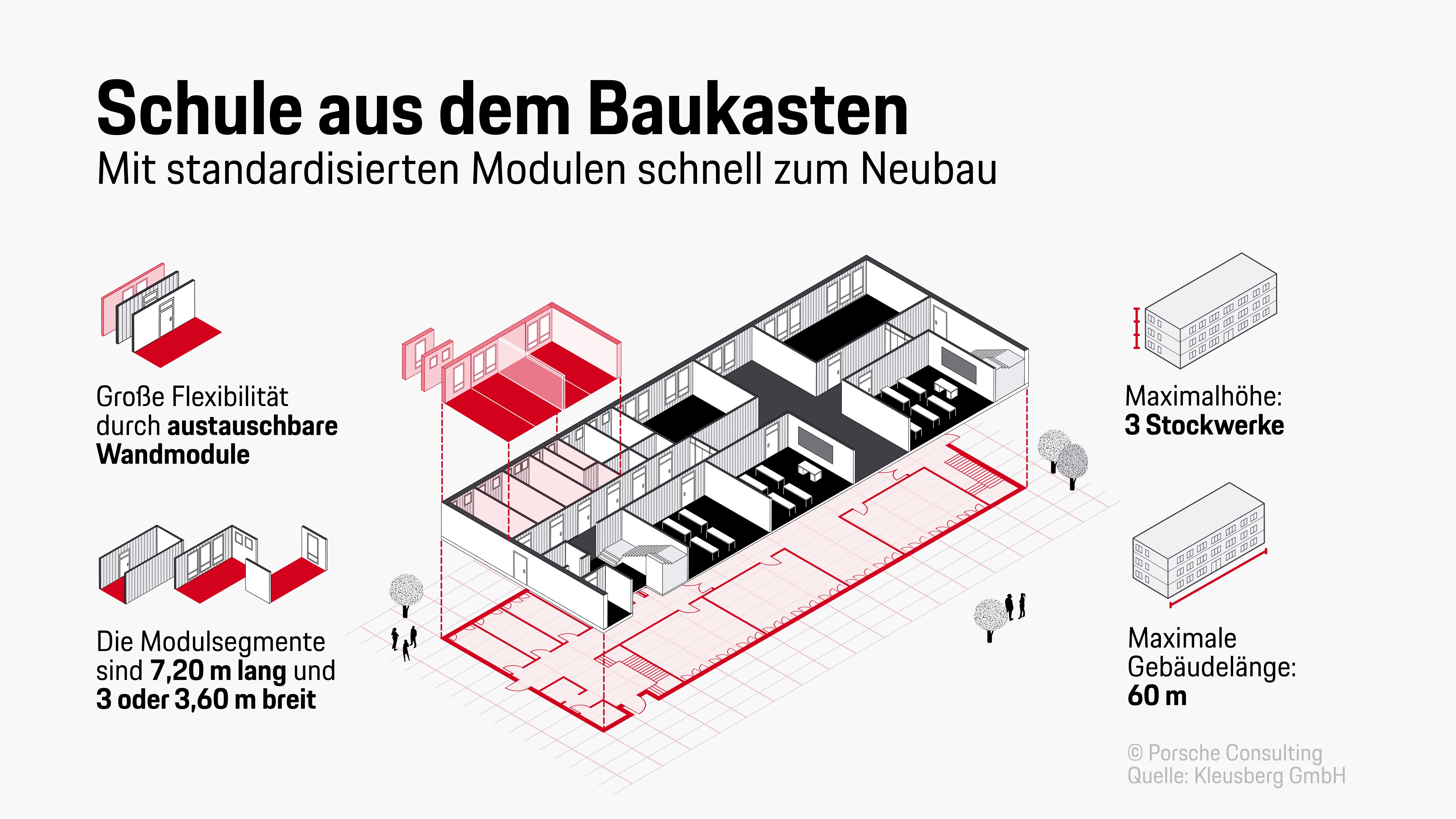
Die Idee dahinter: Schulen sollen in Zukunft – technisch gesehen – nicht mehr als Unikate geplant und gebaut werden, sondern sich einfach aus standardisierten Modulsegmenten konfigurieren lassen. Damit geht Kleusberg einen entscheidenden Schritt über den bereits seit Jahrzehnten etablierten Modulbau hinaus: Aus dem Projekt- wird künftig ein Produktgeschäft. Bauträger können sich neue Schulen dank des Baukastenprinzips aus einem Online-Konfigurator aussuchen und in Auftrag geben – und das, ohne Abstriche bei den Gestaltungsmöglichkeiten machen zu müssen. Alle Anforderungen an die verschiedenen Funktionen einer Schule wurden von Kleusberg während der Produktentwicklung berücksichtigt. Kurz gesagt: Was Schüler und Lehrer nicht sehen, ist standardisiert. Alles andere rund um die Layoutkonfiguration und Ausstattung lässt sich in weiten Grenzen individualisieren.
„Dieser Produktgedanke ist für die Baubranche neu, denn Bauen verlangt eigentlich nach Individualität – unter anderem wegen der jeweiligen Grundstückszuschnitte und der unterschiedlichen Vorgaben in den örtlichen Bebauungsplänen“, erklärt Kleusberg-Geschäftsführer und Architekt Oliver Hartmann (Jahrgang 1970). „Wir arbeiten stattdessen mit 44 vordefinierten Modulsegmenten, mit denen wir fast jede denkbare Konfiguration realisieren können. Das macht es uns möglich, jede Schule trotz Standardisierung exakt an die Wünsche unserer Auftraggeber anzupassen. Wir zielen mit dem Baukasten zunächst auf Schulerweiterungen oder bis zu vierzügige Grundschulneubauten.“
Möglich sind riegel‑, L- oder Z‑förmige Schulgebäude mit vier bis 16 Räumen und maximal drei Stockwerken. Auf rund 500 bis 2.500 Quadratmetern können zwischen 100 und 420 Schülerinnen und Schüler unterrichtet werden – und zwar mit ganz unterschiedlichen pädagogischen Konzepten: Die Modulsegmente des Schulbaukastens lassen sich auf verschiedene Weise kombinieren, sodass klassische Flurschulen mit gleich großen Räumen ebenso realisiert werden können wie Schulen mit unterschiedlich geschnittenen Klassenzimmern oder einer zentralen Mitte, um die sich einzelne Räume gruppieren. So realisiert Kleusberg zeitgemäße Bildungslandschaften – beispielsweise mit Räumen für individualisiertes Lernen oder die Inklusion von Kindern mit Beeinträchtigungen.

Per Konfigurator zum Unikat
Um seinen Kunden die Auswahl zu erleichtern, bietet Kleusberg die vier Ausstattungspakete „Basis“, „Best Seller“, „Design“ und „Natur“ an. Sie unterscheiden sich unter anderem durch die Gestaltung der Beleuchtungselemente, das Material der Fensterrahmen, die eingesetzte Heiztechnik und die Energieeffizienz der Gebäude. Wer sich durch den von Kleusberg verfolgten Paketgedanken und den Schulkonfigurator an die Automobilindustrie erinnert fühlt, ist auf der richtigen Spur. „Wir hatten bei der Produktentwicklung die Autohersteller im Hinterkopf, die aus einer vorgegebenen Palette von Konfigurationsmöglichkeiten höchst individuelle Lösungen erzeugen, ihren Kunden zur Orientierung ebenfalls Ausstattungspakete anbieten und ihre Produkte seriell auf einer Fertigungsstraße produzieren“, sagt Hartmann.

Einen großen Unterschied zur Autoindustrie gibt es aber auch: Es gelten nicht in jedem Bundesland andere Vorschriften für die Zulassung von Fahrzeugen – wohl aber deutschlandweit 16 unterschiedliche Schulbauordnungen. Und so war es eine der größten Herausforderungen bei der Produktentwicklung, allen behördlichen Vorgaben gleichzeitig gerecht zu werden. „Wir wollten einen Schulbaukasten entwickeln, der in allen Regionen funktioniert“, berichtet Jonas Beuth (Jahrgang 1993), der bei Kleusberg die Produktentwicklung leitet. „Darum mussten wir den kleinsten gemeinsamen Nenner aus allen Vorschriften finden.“ Keine leichte Aufgabe, schließlich ist die Zahl der Bauvorschriften in Deutschland allein zwischen 2005 und heute von 5.000 auf 20.000 gestiegen.

Immerhin musste Kleusberg nicht bei null anfangen. Nach über 160 im Projektgeschäft errichteten Schulen in Modulbauweise wusste man dort sehr genau, was sich die öffentlichen und privaten Bauträger wünschen. Außerdem holte sich das Unternehmen Rat bei Architekten, Lehrern und Hausmeistern. „Ein erfolgreicher Übergang zum Produktgeschäft setzt ein tiefes Verständnis des Marktes und der Kunden voraus – insbesondere, wenn der Produktgedanke wie in diesem Fall noch völlig neu ist“, sagt Tobias Michels (Jahrgang 1989), Senior Manager im Bereich Construction & Real Estate bei Porsche Consulting. Mit seinem Team unterstützte er Kleusberg dabei, den Schulbaukasten für den Alltag in den Gebäuden maßzuschneidern. Michels: „Dabei kommt es manchmal auf vermeintliche Kleinigkeiten an: Je nach Platzierung des Lehrerpults im Klassenzimmer kann es zum Beispiel nur zwei oder bis zu zehn Minuten dauern, bis sich die Schüler am Unterrichtsbeginn beruhigen.“
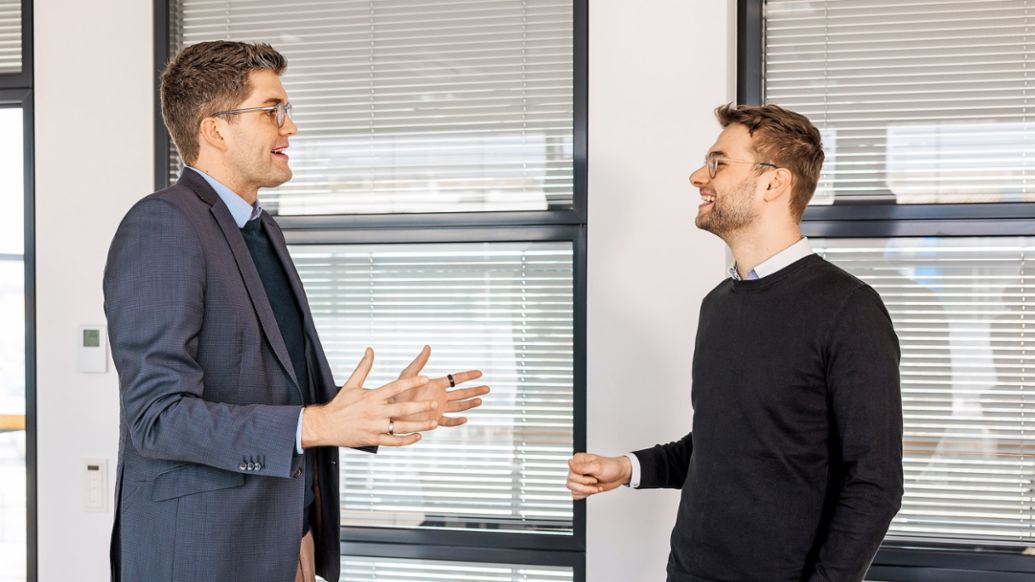
In drei Monaten zur neuen Schule
Eine Zeitersparnis ganz anderer Art ermöglicht die Produktionsweise der Schulbaumodule: Nur drei Monate sollen in Zukunft zwischen Produktionsstart und Schlüsselübergabe vergehen – im konventionellen Schulbau können hingegen schon einmal mehrere Jahre bis zum Einzug vergehen. Möglich macht das die serielle Fertigung der Gebäudebestandteile, die in einer 500 Meter langen Halle auf dem Werksgelände in Kabelsketal-Dölbau stattfindet. Das heißt: Am einen Ende des Gebäudes kommen maßgeschneiderte Stahlprofile für das Tragwerk an, am anderen Ende verlassen pro Woche bis zu 80 komplette Module – bestehend aus den geforderten Segmenten – die Produktionshalle. Dazwischen entstehen an Vorfertigungslinien Komponenten wie Böden, Decken und Wände, die schrittweise an der Grundkonstruktion befestigt werden. Von oben betrachtet erinnert das Layout der Fertigung an eine Fischgräte, weshalb Experten auch vom „Fischgräten-Ansatz“ sprechen – eine weitere Inspiration aus den Fabriken der Automobilindustrie.
Nach ihrer Fertigstellung gelangen die Module des Schulbaukastens per Schwertransport vom ostdeutschen Bundesland Sachsen-Anhalt zu ihren Bestimmungsorten, wo sie von Kleusberg zum Schulgebäude zusammengesetzt werden – im Wesentlichen per „Plug-and-Play“, weil Rohre und elektrische Leitungen schon verlegt sind und nur noch miteinander verbunden werden müssen. Selbst die Toiletten und Waschbecken für WC-Räume sind bereits installiert, wenn die Module an der Baustelle ankommen. „Wegen des hohen Vorfertigungsgrades fällt vor Ort viel weniger Arbeit an“, erklärt Beuth. „Dort kümmern wir uns vor allem um die Flurbereiche, die Modulstöße in den Klassenzimmern, die Fassade und das Dach.“

Keine Verzögerungen, keine Mehrkosten
Die serielle Fertigung spart aber nicht nur Zeit: Wegen der größeren Stückzahlen kann Kleusberg bei seinen Zulieferern, zum Beispiel den Sanitärherstellern, auch günstiger einkaufen und mit Nachunternehmern bessere Konditionen aushandeln, weshalb die Baukosten im Vergleich zum herkömmlichen Projektgeschäft-Modulbau um rund 15 Prozent sinken sollen. Hinzu kommt, dass Kostenexplosionen und Verzögerungen dank des Produktansatzes künftig nahezu ausgeschlossen sein dürften, ebenso wie Qualitätsprobleme: Da die Fertigung unter kontrollierten Bedingungen im Werk abläuft, nach jedem Fertigungsschritt eine Qualitätskontrolle stattfindet und alle Produktexpertinnen und ‑experten bei Fragen schnell greifbar sind, sollten die Module weitgehend gleichbleibende Eigenschaften haben. „Autos kommen ja auch aus einer Fabrik und werden nicht einzeln vor Ort in der Garage des Kunden gebaut – was mit Sicherheit zu sinkender Qualität führen würde“, zieht Architekt Hartmann den nächsten Vergleich mit den Autoherstellern. „Und falls wir in der seriellen Fertigung auf ein Problem stoßen sollten, können wir es schnell erkennen und zuverlässig abstellen.“ Selbst dem zunehmenden Fachkräftemangel auf dem Bau könnte das Konzept entgegenwirken: Immer weniger Menschen wollen bei Wind und Wetter Mauern errichten oder die Außendämmung anbringen. Bei Kleusberg findet die Produktion hingegen hauptsächlich in einer Fabrikhalle statt, was die Attraktivität der Bauberufe deutlich erhöhen könnte.
Die Schule folgt den Schülern
Eine weitere Eigenschaft der Schulen aus dem Baukasten ist den Kleusberg-Entwicklern besonders wichtig: ihre Nachhaltigkeit. Da Außen- und Innenwände sowie Böden und Decken zum größten Teil aus Holz bestehen, weisen die Module eine positive CO₂-Bilanz auf. Sie binden also mehr Kohlendioxid, als bei ihrer Produktion entsteht. Hinzu kommt: Die Module lassen sich auch nach vielen Jahren noch problemlos voneinander lösen und wiederverwenden. „Wenn es in einer Gegend zu wenige Schüler gibt, können wir eine bestehende Schule demontieren und an einer anderen Stelle mit größerem Bedarf neu aufbauen“, so Hartmann. „Nachhaltiger geht es wirklich nicht.“
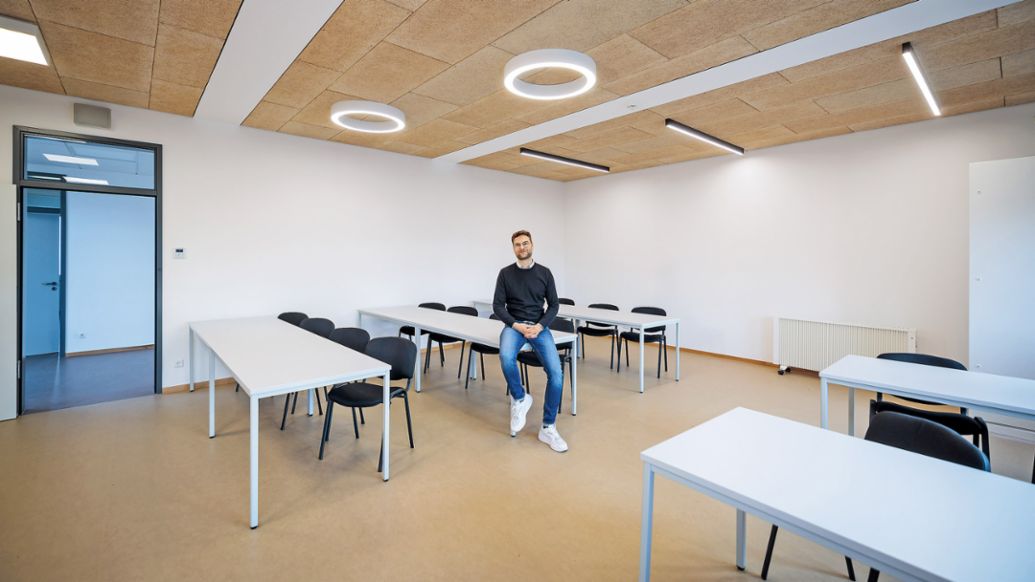
Potenzielle Kunden reagieren bisher sehr positiv auf die Schulbaukasten-Idee. „Zuerst gibt es oft eine gewisse Skepsis, weil wir den konventionellen Weg verlassen“, berichtet Beuth. „Bisher konnten wir aber alle Bedenken ausräumen und Interessenten vom Schulbaukasten überzeugen. Denn Vorteile wie eine kurze Bauzeit und Kosteneinsparungen überzeugen die Bauträger.“ Und deren Bedarf ist groß: Die KfW-Bankengruppe, eine staatliche Förderbank, hat Schulgebäude als den größten Investitionsbereich der Kommunen in Deutschland identifiziert und schätzt, dass rund 47 Milliarden Euro in den Neubau und in die Modernisierung bestehender Schulen fließen müssen. Hinzu kommt, dass die Zahl der Schülerinnen und Schüler bis 2030 um rund neun Prozent steigen wird – eine Zunahme um rund eine Million.
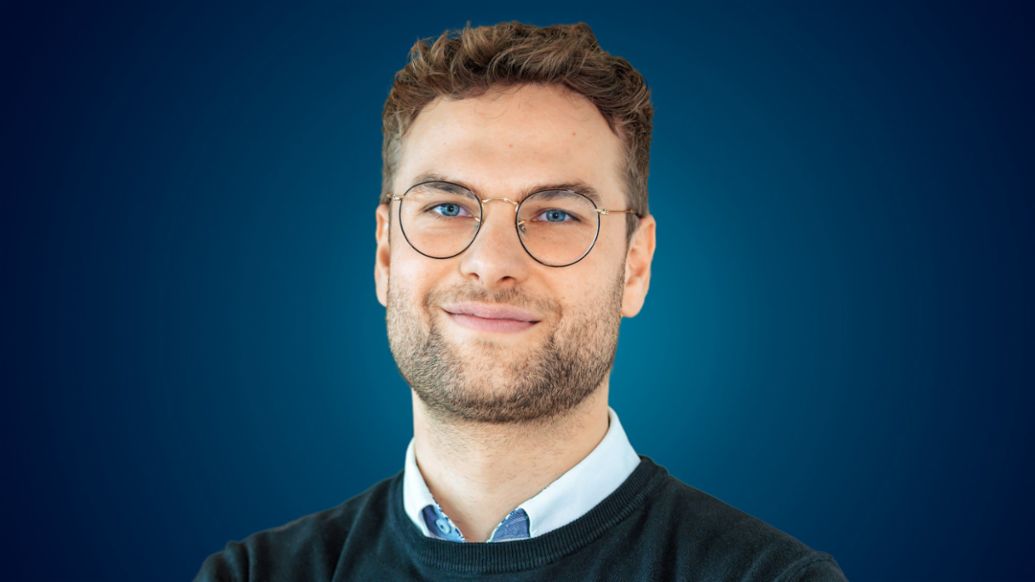
Die Idee ist übertragbar
Kein Wunder also, dass Kleusberg bereits mit ersten Kunden einig geworden ist. Ziel des Unternehmens ist es, in den nächsten Monaten weitere Auftragseingänge für den Schulbaukasten zu verzeichnen. Und natürlich denken die Produktentwickler bereits über diesen ersten Markt hinaus – denn die Idee hinter dem Schulbaukasten lässt sich auch auf den Bau von beispielsweise Bettenhäusern in Kliniken, Studentenwohnheimen oder Unterkünften für Geflüchtete übertragen. Es wäre darum keine Überraschung, wenn auf das serielle Klassenzimmer bald noch viele andere maßgeschneiderte Gebäude aus einem Kleusberg-Konfigurator folgen würden.
Kleusberg GmbH: Den Anfang macht eine Schreinerei
Seit 1948 ist Kleusberg im Baugewerbe aktiv. Entstanden aus einer Bau- und Möbelschreinerei, entwickelte sich das Unternehmen zunächst zum Hersteller von Bauwagen, später von Baucontainern – genutzt für mobile Büros auf Baustellen, aber auch als temporäre Lösung für Schulen oder Kindergärten. Inzwischen hat Kleusberg 35.000 solcher Mietcontainer im Angebot.
Zweites Standbein ist der Modulbau, der sich Ende der 80er-Jahre des vergangenen Jahrhunderts aus der sogenannten Stahlverbundsystembauweise entwickelt hat. Seit mehr als 30 Jahren errichtet Kleusberg im Projektgeschäft Schulen, Kindergärten, Bürogebäude und Krankenhäuser aus vorgefertigten Modulen für die dauerhafte Nutzung. Nun kommen Schulbauten als Produkte aus Standardmodulen hinzu.
Die Kleusberg GmbH ist noch immer ein Familienunternehmen und beschäftigt 1.400 Menschen an 13 Standorten in Deutschland.
Kommentar: Perspektive mit Potenzial
Von Tobias Michels, Senior Manager, Porsche Consulting
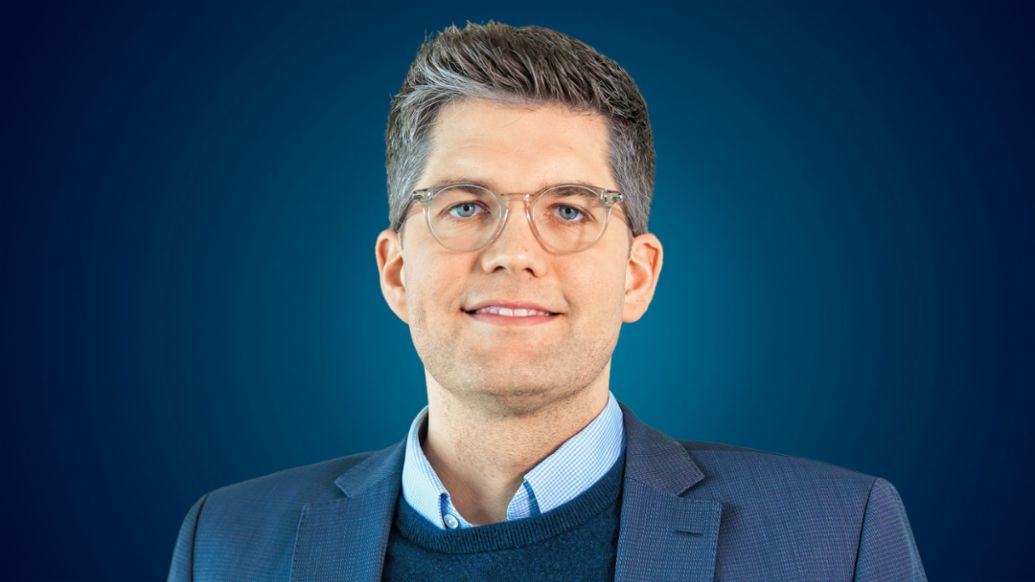
In der gegenwärtigen Wirtschaftslage – geprägt von Inflation sowie steigenden Baupreisen und Zinsen – steht die Bauindustrie vor großen Herausforderungen. Der deutliche Rückgang der Baugenehmigungen signalisiert einen kritischen Wendepunkt, und es zeichnet sich ab, dass kurz- bis mittelfristig keine wesentliche Besserung in Sicht ist. Es ist offensichtlich, dass die Hoffnung auf staatliche Unterstützung allein keine nachhaltige Strategie sein kann. Stattdessen müssen die Unternehmen ihre Geschäftsmodelle grundlegend überdenken und an die neuen Marktbedingungen anpassen. Besonders das traditionelle, margenschwache Projektgeschäft steht auf dem Prüfstand.
Ein Beispiel für eine gelungene strategische Neuausrichtung ist Kleusberg. Trotz bereits bestehender Aktivitäten im Modulbau konnte das Unternehmen die Vorteile des industriellen Bauens nicht voll ausschöpfen – bedingt durch den projektbasierten Charakter des bisherigen Geschäfts.
Produkte statt Projekte
Die Lösung: der Übergang zum Produktgeschäft. Hier sind allerdings frühzeitige Entscheidungen über Zielmärkte wichtig, um länderspezifische regulatorische Anforderungen (zum Beispiel Bauordnungen) bereits in der Produktentwicklungsphase berücksichtigen zu können. Es ist zudem kritisch, die Bedürfnisse sowohl der Eigentümer als auch der Endnutzer zu verstehen. Nur dann kann man maßgeschneiderte Lösungen anbieten, die sich in der Betriebsphase bewähren.
Die Entwicklung dieser modularen Produkte verlangt einen ganzheitlichen Ansatz, der Fertigung, Lieferung und Montage umfasst. Ein gut durchdachtes modulares Bau- und Produktionssystem – bestehend aus clever konzipierten, vorgefertigten Modulen – erhöht nicht nur die Qualität, sondern beugt auch Schnittstellenproblemen vor. Zudem adressiert es den Fachkräftemangel, die Materialknappheit sowie wetterbedingte Verzögerungen. Und schließlich gewährleistet es die Einhaltung des vereinbarten Budgets.
Die Transformation vom projektbasierten zum produktorientierten Geschäftsmodell bringt aber auch tiefgreifende Veränderungen für ein Unternehmen mit sich. Wurden Gebäude bisher auf Basis individueller Leistungsvereinbarungen geplant, müssen nun Expertinnen und Experten produktoptimierte Lösungen erarbeiten. Der Vertrieb, der bisher reaktiv auf Ausschreibungen reagiert hat, muss nun proaktiv das Produkt am Markt positionieren. Der Einkauf, der bisher projektspezifisch agiert hat, kann nun langfristige Partnerschaften für das Seriengeschäft etablieren. Man sieht: Die Einführung eines neuen Produkts erfordert eine unternehmensweite Strategie, die sämtliche Funktionen und Prozesse umfassen und von der Geschäftsführung klar vorgegeben werden muss.
Das Beispiel Kleusberg verdeutlicht, dass der Übergang zum Produktgedanken nicht nur theoretisch möglich ist, sondern auch praktisch erfolgreich umgesetzt werden kann. In einer Zeit, in der die Bauindustrie sich neu erfinden muss, bieten Modularisierung und industrielles Bauen eine vielversprechende Möglichkeit, auf die aktuellen Herausforderungen zu reagieren und zugleich Effizienz und Kundenzufriedenheit zu steigern. Unternehmen, die Modularisierung und industrielles Bauen heute als Chance sehen, werden darum in Zukunft die Gewinner sein.
Info
Text erstmalig erschienen im Porsche Consulting Magazin.