The future of school construction stands next to the parking lot for plant 2 at Kleusberg, a module-manufacturing company in the eastern German town of Kabelsketal near the city of Halle/Saale. This prototype building is a single-story rectangle with a flat roof and wooden façade. It is a product of the company’s “school construction kit,” whose predefined modules enable shorter construction times while maintaining or increasing architectural flexibility. The prototype consists of a modern classroom, auxiliary rooms, and sanitary facilities. In addition to their shorter construction times, the company’s new schools also score points for sustainability. If needed they can be moved to new locations, and are nearly 100 percent recyclable at the end of their service lives. Kleusberg and the Porsche Consulting management consultancy present a jointly developed need-based and sustainable concept here. Long-standing problems in the construction industry thus appear to be solvable.
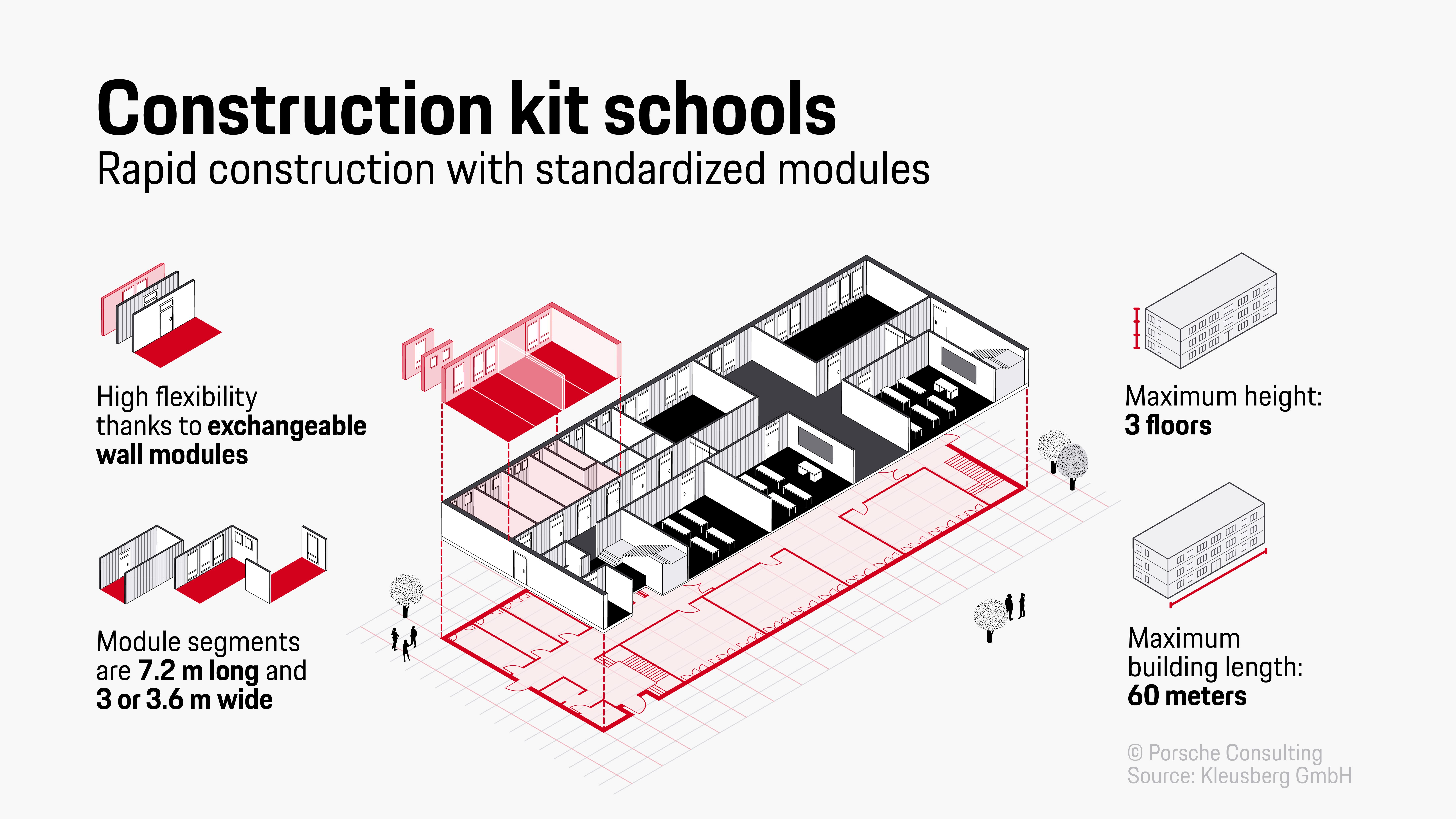
The underlying idea is the following: schools of the future should no longer be planned and built as unique projects — in purely technical terms — but rather be easily configured from standardized module segments. Kleusberg is therefore taking a decisive step beyond the type of modular construction that has existed for decades: it is transitioning from a project- to a product-based business model. Thanks to its modular design principle and online configurator, developers can select and commission their new schools without having to sacrifice any design possibilities. Kleusberg takes all the requirements for a school’s different functions into account during the product development phase. In short, it standardizes the parts that the students and teachers do not see. Everything else related to the layout configuration and interiors can be individualized within wide limits.
“This product-based approach is new for the industry. Construction generally calls for individuality — for many reasons, including individual site properties and differences in local zoning and development plans,” explains Oliver Hartmann (born in 1970), an architect and Kleusberg’s CEO Modular Construction. “Instead, we work with 44 predefined module segments that allow for just about any conceivable configuration. Despite the standardization, that enables us to fulfill our clients’ exact wishes. Right now we’re using our modular approach for school extensions and for new primary school buildings with up to four classrooms per grade.”
Rectangular, L‑, or Z‑shaped school buildings with four to 16 classrooms and up to three floors are possible. They can have approximately 500 to 2,500 square meters and accommodate 100 to 420 students — for very different educational strategies. The module segments can be combined in different ways, enabling traditional layouts with same-sized classrooms off a corridor as well as layouts with differently sized classrooms or a central space with individual rooms grouped around it. Kleusberg can therefore construct contemporary educational landscapes — including rooms for individualized instruction, for example, or for the inclusion of children with special needs.

Unique creations from a configurator
To simplify its clients’ selection procedure, Kleusberg offers four packages: Basis, Best Seller, Design, and Nature. They differ in the design of their lighting elements, for instance, as well as their window frame materials, type of heating system, and energy efficiency. Those who associate Kleusberg’s package approach and configurator with the automotive industry are on the right track. As Hartmann notes, “When developing our products we did have carmakers in the back of our minds. They, too, can offer highly individualized solutions from a predetermined range of configurational possibilities, guide their customers with package options, and use series production lines to make their products.”

Yet there is one major difference to the automotive industry: Germany’s 16 states follow a single set of regulations for vehicle authorizations — but each has its own set of regulations for building new schools. As such, one of the biggest challenges for product development consisted of meeting all of these official requirements at the same time. “We wanted to develop a school construction kit that functions in every region,” says Jonas Beuth (born in 1993), Kleusberg’s Head of Product Development, Modular Construction. “We therefore had to find the lowest common denominator for all of the regulations.” Not an easy task. For one thing, the number of building regulations in Germany has risen from 5,000 to 20,000 from 2005 to today alone.

Nevertheless, Kleusberg did not have to start from square one. Having already built more than 160 schools with a modular system and project-based approach, it was very well acquainted with the wishes of both state and private clients. The company also sought input from architects, teachers, and building caretakers. “Successfully transitioning to a project-based business model requires a deep understanding of the market and customers — especially if the product idea is completely new, as is the case here,” says Tobias Michels (born in 1989), Senior Manager in Construction & Real Estate at Porsche Consulting. Michels and his team supported Kleusberg in tailoring the school construction toolkit to meet everyday school-building needs. “Sometimes it comes down to what can seem like details,” he observes. “For example, the location of the teacher’s desk can affect whether it takes only two or as many as ten minutes for the students to settle down and start concentrating on their lessons.”
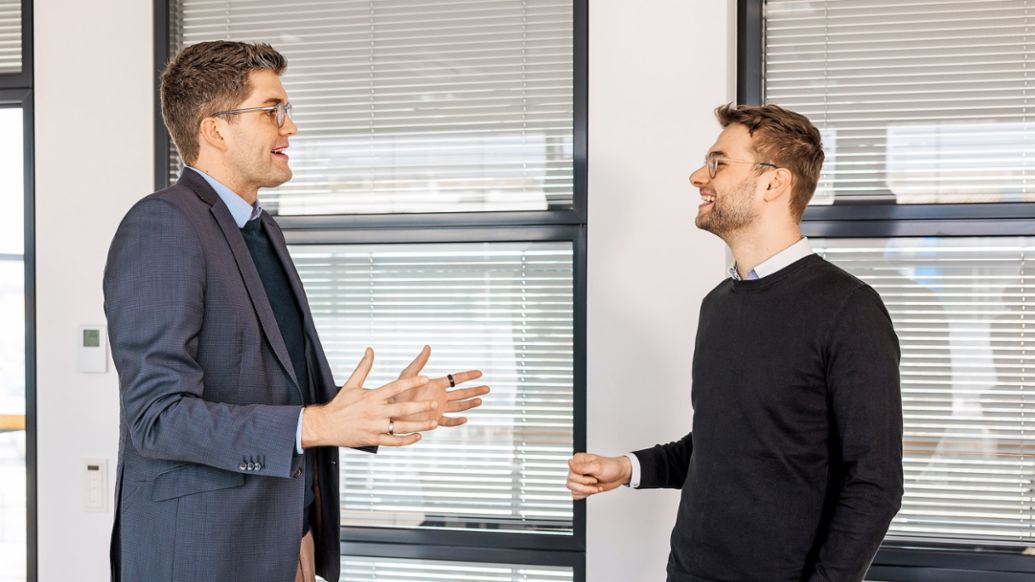
Three months for a new school
The school modules are manufactured in a way that opens entirely new horizons for saving time. In the future, just three months should transpire from start of production to handing over the keys. By contrast, conventional school construction projects can take several years before the building is ready for use. Series production of the building components, which is done in a 500-meter hall at Kleusberg’s plant in Kabelsketal-Dölbau, is what makes it possible to shorten the time. Pre-specified steel beams for the bearing structure are delivered to one end of the hall. At the other end, up to 80 complete modules — each with the requisite segments — leave the hall every week. Pre-production lines assemble components such as floors, ceilings, and walls, which are installed in the basic structure on a step-by-step basis. Viewed from above, the layout has a “herringbone” character, leading some experts to in fact call it that — which is yet another inspiration from factories in the automotive industry.
When the modules are completed, heavy-duty vehicles transport them from the eastern German state of Saxony Anhalt to their respective destinations, where Kleusberg then assembles them into a school building — primarily using a plug-and-play principle, because the pipes and electrical lines have already been laid and only need to be connected. Even the toilets and sinks for the sanitary facilities have already been installed when the modules reach their sites. “The high degree of prefabrication means there’s a lot less to do at the site itself,” explains Beuth. “That’s where we concentrate on the corridor areas, classroom module interfaces, façades, and roofs.”

No delays, no added costs
Series production not only saves time. Because of the high piece numbers, Kleusberg can purchase items such as bathroom fixtures at lower rates and negotiate better conditions with subcontractors. This is expected to lower costs by around 15 percent compared to a project-based approach. Moreover, a product-based approach should nearly eliminate cost explosions and delays, as well as quality issues. With production taking place under controlled conditions at the plant, including quality checks at every step, and with all the product experts there and quickly available for questions, the modules should have largely uniform qualities. “Cars, after all, also come from a factory and are not constructed individually in each customer’s garage — which would surely lower their overall quality levels,” says Hartmann, drawing another comparison with the automotive industry from an architect’s perspective. “If a problem should occur in our series production, we can quickly identify it and take reliable corrective action.” The product approach can even help to counter the growing shortage of skilled construction workers. Fewer people are eager to build walls or apply exterior insulation in any and all weather conditions. At Kleusberg, however, most production takes place in a factory hall, which could considerably raise the appeal of jobs in the industry.
Schools can follow their students
This approach to building schools offers yet another benefit that is especially close to the hearts of Kleusberg’s developers, namely sustainability. Because the exterior and interior walls as well as floors and ceilings are made largely of wood, the modules have a positive carbon footprint. They bind more carbon dioxide than arises in their production. In addition, after many years of use, the modules can be easily taken apart and used elsewhere. “If a particular region no longer has enough students, we can dismantle the school and set it up where there’s a greater need,” says Hartmann. “You can’t really get any more sustainable than that.”
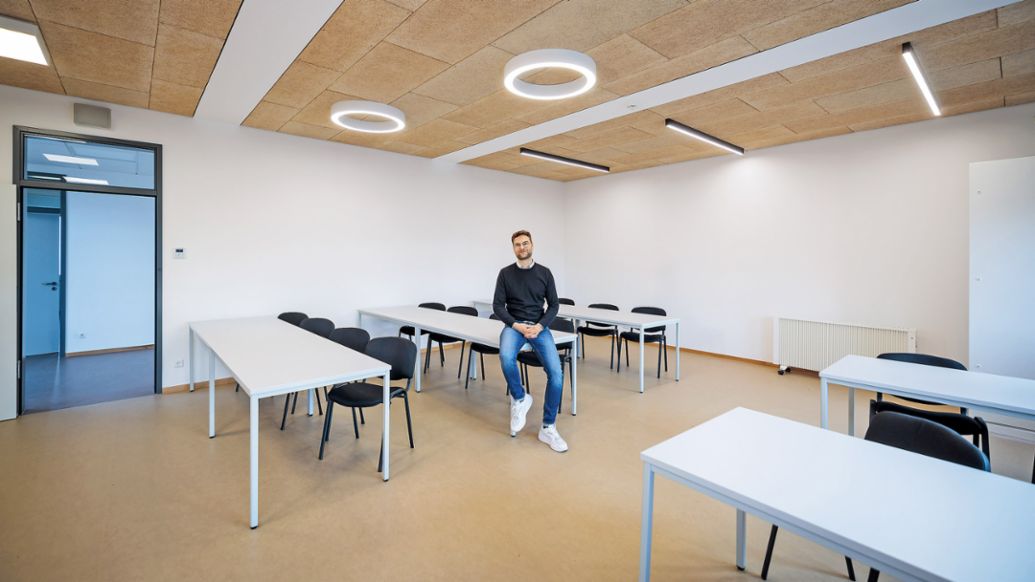
Potential customers have been responding very positively to the school construction kit idea. “There’s often a little skepticism at first because we’ve departed from the conventional path,” says Beuth. “But thus far we’ve been able to address all the concerns and convince any interested parties. Advantages such as short construction times and lower costs are very appealing to builders.” And there is a big need. The KfW bank group, a state-owned development bank, expects school buildings to be the largest field of investment for municipalities in Germany. It estimates that around 47 billion euros need to go into building new schools and modernizing existing ones. In addition, by 2030 the number of schoolchildren is expected to rise by about nine percent, an increase of around one million pupils.
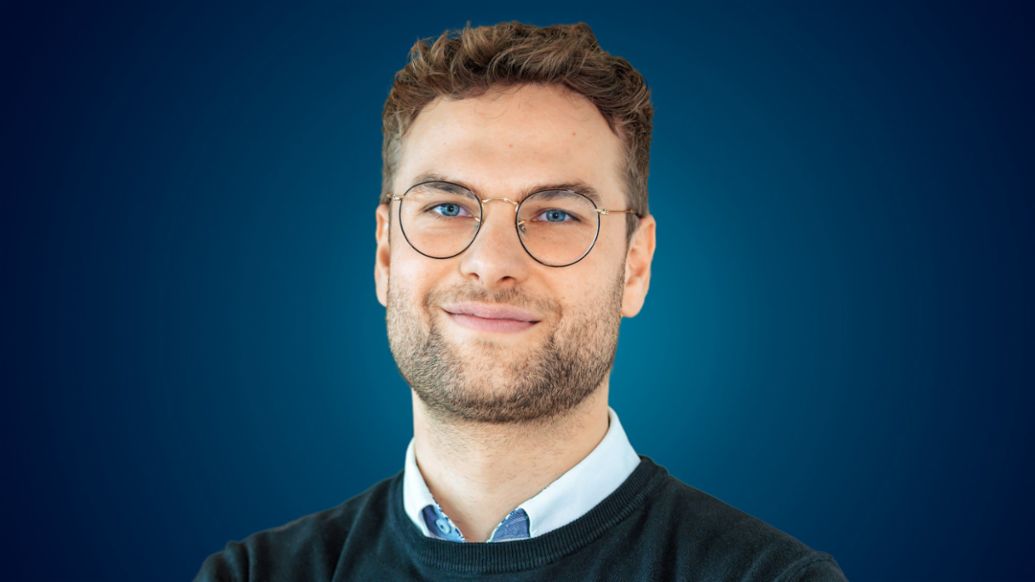
The idea is transferrable
It’s therefore no wonder that Kleusberg has already reached agreements with its first customers. Over the coming months, the company aims to bring in more orders for its modular schools. Its product developers are naturally also thinking beyond this initial market, because the idea behind the schools is transferrable to buildings such as hospital wards, college dormitories, and refugee housing. It should come as no surprise, therefore, if Kleusberg’s series-production classrooms are followed by many other tailor-made buildings from the company’s configurator.
Kleusberg GmbH: It started with a carpenter’s shop
Kleusberg entered the building industry back in 1948. Originally a carpenter’s shop for construction and cabinetry, it began by making construction trailers, then construction cabins as mobile on-site offices but also as temporary solutions for schools or daycare centers. Kleusberg currently has 35,000 of these cabins for rent.
The company’s second pillar is its modular construction, which it developed from a steel composite system in the late 1980s. For more than 30 years, Kleusberg has been making permanent schools, daycare centers, office buildings, and hospitals from prefabricated modules using a project-based approach. Now, it is offering school buildings as products made of standard modules.
Kleusberg GmbH remains a family business, with 1,400 employees at 13 locations in Germany.
Commentary: Prospect with Potential
By Tobias Michels, Senior Manager, Porsche Consulting
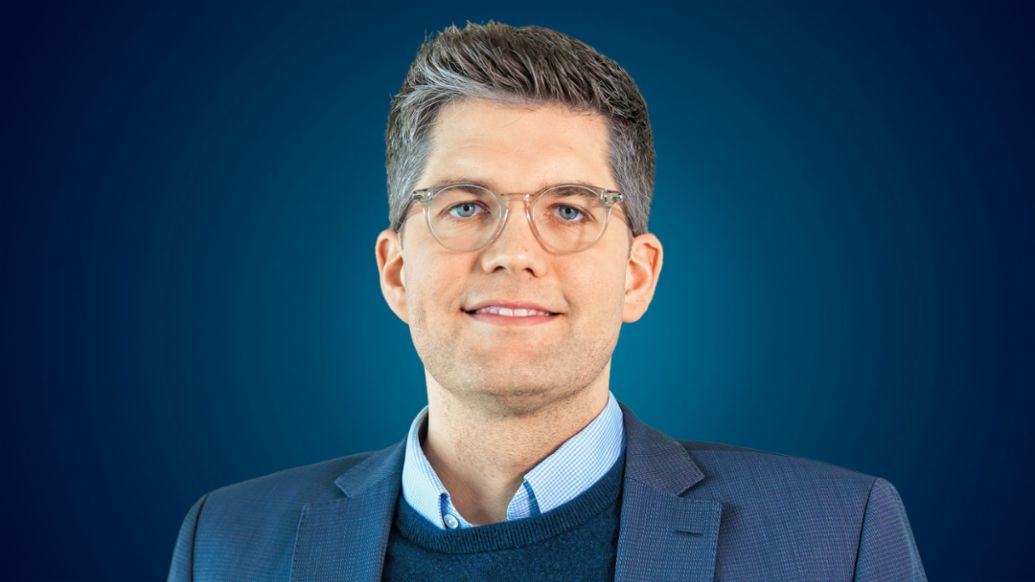
The current economic climate — marked by inflation as well as rising construction costs and interest rates — is posing major challenges to the construction industry. A significant decline in the number of building permits is signaling a critical turning point, with no signs of any meaningful short- or medium-term improvement in sight. Clearly, a sustainable strategy cannot consist of hope and government support alone. Instead, some companies need to fundamentally rethink their business models and adapt to the new market conditions. In particular, the traditional, low-margin, project-based business model needs to be reevaluated.
Kleusberg is an example of a company that has succeeded in taking a strategic new course. Although it had already worked with modular construction, it had not been able to take full advantage of industrial construction — due to the project-based nature of its previous business.
Products over projects
The solution: shifting to a product-based business model. This, however, requires selecting target markets early on in order to take country-specific regulatory requirements (such as building codes) into account as early as the product development phase. It is essential to understand the needs of both the owners and the end users. Only then is it possible to provide customized solutions that prove themselves in practice.
Developing these modular products requires an overall approach that covers manufacture, delivery, and assembly. A well-thought-out modular construction and production system — consisting of cleverly designed, prefabricated modules — not only increases quality but also guards against interface problems. Furthermore, it addresses skilled labor shortages, material scarcity, and weather-based delays. And finally, it ensures that budget agreements can be met.
It should be noted, however, that transitioning from a project- to a product-oriented business model also brings extensive changes to the company itself. Whereas buildings used to be planned on the basis of individual contracts, company experts now need to produce product-optimized solutions. Sales departments, which previously responded to calls for tenders, now need to position their products proactively on the market. Procurement, which used to act with respect to specific projects, can now establish long-term partnerships for ongoing series production. As is evident, introducing a new product requires a company-wide strategy that extends across all functions and processes and needs to be clearly defined by top management.
Kleusberg’s example shows that transitioning to a product approach is not only possible in theory but can also be successfully applied in practice. At a time when the construction industry needs to reinvent itself, modularization and industrial construction offer a promising chance to tackle current challenges and also increase efficiency and customer satisfaction. Companies that view modularization and industrial construction as opportunities today will come out ahead of the game in the future.
Info
Text first published in Porsche Consulting Magazine.