Serienmanufaktur
Anfänge in Zuffenhausen
„Am Anfang schaute ich mich um, konnte aber den Wagen, von dem ich träumte, nicht finden: einen kleinen leichten Sportwagen, der die Energie effizient nutzt. Also beschloss ich, ihn mir selbst zu bauen“, sagte Ferry Porsche. Über die klare Vorstellung hinaus, wie der erste Sportwagen der Marke Porsche auszusehen hat, steht für den Unternehmensgründer von Beginn an die Produktion im Mittelpunkt. Die Anfänge sind durch die frühe Nachkriegszeit geprägt. So entstehen ab 1948 der Porsche 356 „Nr. 1“ Roadster und eine Kleinserie von 52 ebenfalls manuell gefertigter Heckmotor-Sportwagen der Baureihe 356. Als Produktionsstätte dient ein zur Werkstatt umfunktioniertes Sägewerk im österreichischen Gmünd. Die Porsche-Mitarbeiter können auf wenige, durch die Kriegswirren gerettete Maschinen zurückgreifen. In erster Linie ist ihr handwerkliches Geschick gefragt. Da dort eine Serienfertigung nicht möglich ist, organisiert Ferry Porsche bereits 1949 den Umzug nach Stuttgart-Zuffenhausen, seit 1938 Sitz des von Ferdinand Porsche 1931 gegründeten Konstruktionsbüros. Gemeinsam mit dem Stuttgarter Karosseriewerk Reutter beginnt 1950 die Serienproduktion des 356. Zu den verschiedenen Investitionen in den fünfziger Jahren zählt 1953 der Bau einer modernen Lackiererei. 1956 entstehen zwischen 18 und 20 Karosserien am Tag.
Bis weit in die sechziger Jahre hinein wird auf engem Raum in unmittelbarer Nachbarschaft der einzelnen Gewerke gearbeitet. Die Produktion verfügt über einen Manufaktur-Charakter. Dahinter verbergen sich klare Ideen einer effizienten Fertigung. Kurze Wege für die einzelnen Bauteile, Sauberkeit und Ordnung sowie das profunde Können der Mitarbeiter werden zum Fundament für die bis heute weltweit hoch geachtete Porsche-Qualität.
Der Blick in die Produktion zeigt aber auch, wie die Karosserien aus einzelnen gebogenen und gepressten Blechen in Handarbeit verschweißt werden. Dazu kommt vor dem Lackieren noch das Hobeln und Verzinnen der Schweißnähte. So wird jede Karosserie zu einem Unikat. Und auch an anderer Stelle sind Ablauf und Ergonomie noch weit von heutigen Standards entfernt. Ein Beispiel dafür ist der Getriebeeinbau beim 356: Hierfür nehmen drei Kollegen das mit der Achse vormontierte Bauteil in die Hand. Einer von ihnen lässt sich rücklings auf den Boden unter das aufgebockte Heck des Fahrzeugs rollen, stemmt das Getriebe mit dem Schienbein in Richtung Fahrzeugboden und – während seine beiden Kollegen das Bauteil an den Achshälften halten – verschraubt es mit dem Wagen. Anfang der sechziger Jahre 30 Mal am Tag. Die vormontierten und lackierten Karosserien werden auf dem Fabrikgelände mit elektrischen Gepäckkulis – wie sie damals sonst auf Bahnsteigen zum Einsatz kommen – bewegt. In der Montage ruhen sie auf Rollwagen, die händisch von einem Montagebereich zum nächsten geschoben werden. Eine Wagenbegleitkarte enthält die notwendigen Informationen über Farbe, Innenausstattungsdetails, georderter Extra-Ausstattung und weiterer individueller Kundenwünsche. Damit ist bereits damals sichergestellt, dass jeder Kunde seinen ganz individuellen Porsche erhält.
Wachstum am laufenden Band
Arbeitsteilige Serienproduktion
1969 – sechs Jahre nach der Messepremiere des 911 – zieht die Sportwagen-Montage in neue Räumlichkeiten. Längst sind die beiden Sheddachhallen im Werk 2 zu eng für die Produktion der weltweit beliebten Sportwagen. Durch den Kauf des Karosseriespezialisten Reutter verfügt Porsche seit Ende 1963 über einen eigenen Karosseriebau. Das neue Montagegebäude an der Schwieberdinger Straße bietet Platz auf drei Etagen. Im zweiten Obergeschoss werden die Karosserien komplettiert, im Stockwerk darunter befindet sich die Endmontage und im Erdgeschoss Qualitätssicherung und Endabnahme. Diese Aufteilung hat sich bis heute bewährt.
Die Einrichtung des Gebäudes folgt dem Gedanken des Fertigungsflusses und das Fließband erhält Einzug. Mittlerweile sind die einzelnen Gewerke – wie Karosseriebau, Sattlerei, Motorenbau und Montage – räumlich voneinander getrennt und sauber strukturiert. Das schafft Raum den Fertigungsfluss zu optimieren. Damit steigen auch die Produktionskapazitäten. So ist es jetzt möglich täglich 50 Karosserien zu produzieren und 86 Fahrzeuge zu montieren. Um darüber hinaus gehende Stückzahlen zu realisieren, hat sich die Zusammenarbeit mit namhaften Zulieferern, wie dem Karosseriebauer Karmann in Osnabrück, etabliert. Dort wird neben den Karosserien für 911 und 914 auch die vierzylindrige Version des 1969 vorgestellten Mittelmotor-Sportwagens montiert. Das sechszylindrige Schwestermodell entsteht in Zuffenhausen. Dem 914 folgen die vierzylindrigen Transaxle-Modelle 924 und 944. Ihre Fertigung gibt Porsche nach Neckarsulm. Der 1977 erscheinende 928 entsteht wiederum am Stammsitz.
Bereits in den sechziger Jahren ist absehbar, dass die elektronische Datenverarbeitung eine zunehmende Rolle spielen wird. Die Namensgebung des 911 ist – abgesehen von dem Wechsel der Bezeichnung von 901 auf 911 – auch der Tatsache geschuldet, dass Porsche traditionell das Händler- und Servicenetz von Volkswagen nutzt. Dort sind für die Ersatzteilorganisation und -logistik alle anderen 100er Zahlenkennungen durch Modelle anderer Marken belegt. Dementsprechend entschließt sich Porsche zur Nutzung der 900er Ziffern.
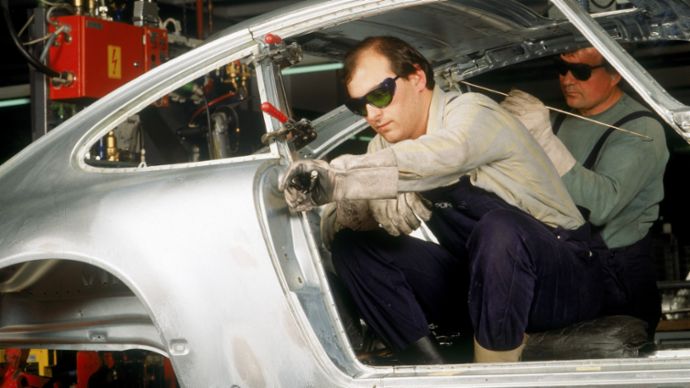
Produktion und Fertigungsprozess verschmelzen zunehmend miteinander. Ein Beispiel dafür liefert die Karosseriestruktur des 911, bei dem – anders als beim 356 – die vorderen Kotflügel mit dem Wagenkörper verschraubt werden. Noch legen Porsche-Mitarbeiter im Karosseriebau Hand an, um die großformatigen Bleche, wie Dach und Wagenboden, zusammenzusetzen. Neben dem Fließband kommen weiterhin Montageschlitten zum Einsatz, mit denen die in Produktion befindlichen Fahrzeuge von Hand zu den einzelnen Montagestationen geschoben werden. Weiterhin zählt bei Porsche Pragmatismus: Um das Einpressen von Gummilagern in die Achsaufhängung zu vereinfachen wird zum Beispiel handelsübliche Hautcreme verwendet.
Das Können der Kollegen bleibt Garant für die geschätzte Qualität der Fahrzeuge. Mit Innovationen, wie der Verwendung feuerverzinkter – und damit rostfreier – Karosseriebleche setzt Porsche Mitte der 1970er Jahre weitere Standards in Sachen Nachhaltigkeit.
Effizienz und Ergonomie mit Roboterhilfe
Automatisierung der Produktionsanlagen durch den Einsatz von Elektronik und IT
Bei Großserienherstellern steigt bis in die achtziger Jahre die Automatisierung. In der Produktion kommen immer mehr Roboter zum Einsatz. Doch ein hoher Automatisierungsgrad ist kein Erfolgsgarant. In puncto Automatisierungsgrad hat Porsche Ende der achtziger Jahre Nachholbedarf. Anfang der neunziger Jahre holt Porsche Produktionsspezialisten aus Japan ins Haus um versäumte Schritte nachzuholen, die die Marke zwischenzeitig in wirtschaftlich bewegte Zeiten brachten. Hieraus entwickelt sich der Porsche-Verbesserungs-Prozess (PVP), der schon kurze Zeit darauf auch in Fernost als Benchmark gilt. Porsche steht fortan für vorbildliche Effizienz und mustergültige Qualität. Der „Lean Turnaround“ macht Porsche schnell wieder profitabel und fit für die Zukunft.
1985 erfolgt der Ausbau der Montage, in der heute noch die zweitürigen Sportwagen vom Band laufen. Die Produktion erfolgt nun im Zweischichtbetrieb. In dem Jahr wächst die Zahl der Porsche-Mitarbeiter um 1.403 auf 7.915. Ziel ist damals der Sprung von 81 auf 100 Fahrzeuge pro Tag. Im folgenden Jahr wird eine neue Lackiererei in Betrieb genommen. Bei ihrer Planung spielen sowohl die mitarbeiterfreundliche Ausgestaltung der Arbeitsplätze als auch der Umweltschutz eine wichtige Rolle. Der Transport der lackierten Karosserien in die Montage erfolgt vollautomatisch über eine verbindende Fördertechnik, die die vollen Straßen in Zuffenhausen entlastet. Von nun an gehört eine Kathodische-Tauchlackierung (KTL) ebenso zum Standard, wie Beschichtungen mit geringerem Lösungsmittelanteil und weitere umweltfreundliche Prozesse. Und auch Roboter erhalten Einzug bei Porsche: In der Lackiererei übernehmen sie den Auftrag des PVC-Unterbodenschutzes. Pünktlich zur Premiere des Typ 964, der dritten Generation des 911, wird der neue Karosseriebau in Betrieb genommen.
-Produktion-in-Stuttgart-Zuffenhausen-1991.jpeg/jcr:content/b-911%20(964)%20Produktion%20in%20Stuttgart-Zuffenhausen%201991.jpeg)
15 Jahre später produziert Porsche in Zuffenhausen täglich 110 Fahrzeuge der Baureihe 911 und 40 Boxster. Im Karosseriebau kommen mittlerweile 105 Schweißroboter zum Einsatz. Dennoch bleibt auch dort weiterhin handwerkliches Knowhow gefragt. Der Sportwagenbauer beschreibt einen Produktionsweg, bei dem die Automatisierung den Menschen unterstützt, der weiterhin im Mittelpunkt steht. Das Unternehmen erlangt nicht nur dank der Leistungsfähigkeit und Performance seiner Sportwagen Weltruf, sondern auch durch effiziente Produktionsprozesse, das akribische Zusammenspiel von Partnern, Zulieferern und Logistik sowie der auf die Produktion ausgerichteten Fahrzeugentwicklung. Porsche perfektioniert in Zuffenhausen sein System der Linienfertigung, bei der einer Perlenkette gleich verschiedene Baureihen und Modelle in bunter Reihenfolge über dasselbe Band laufen. Anfangs sind das die Modelle 928 und 911. Heute sämtliche Varianten des 911 – inklusive seiner Motorsportderivate – sowie die Modelle Cayman und Boxster der Baureihe 718.
Als 2002 mit dem Cayenne zu 911 und Boxster eine dritte, 2009 mit dem Panamera eine vierte mit dem Macan 2014 gar eine fünfte Modellreihe hinzukommen, expandiert Porsche in Leipzig. Mitten in Deutschland entsteht eine moderne Fabrik in verkehrsgünstiger Lage, mit kurzen Wegen, optimalen Produktionsprozessen und Naturschutzmaßnahmen. Nachhaltigkeit wird auch hier großgeschrieben.
Eine Fabrik der Zukunft
Hand in Hand – Flexibel und effizient dank einer intelligent vernetzten Fertigung

Mit Beginn der Produktion des Taycan, dem ersten Elektro-Porsche, macht das Unternehmen einen großen Schritt in Richtung „Fabrik der Zukunft“. Insgesamt investiert das Unternehmen bis 2022 sechs Milliarden Euro in die Elektromobilität. Über 700 Millionen davon werden für den Aufbau der Taycan-Produktion in Zuffenhausen verwendet. Die Belegschaft beteiligt sich durch ein Mitarbeiterpaket an diesem Zukunftsbekenntnis der Marke zum Traditionsstandort.
„Der Mensch steht bei Porsche weiterhin im Mittelpunkt. Wir bauen Fahrzeuge von Menschen für Menschen.“ Albrecht Reimold, Mitglied des Vorstandes Produktion und Logistik
Die Produktion in der neuen Fabrik steht unter dem Schlagwort Porsche Produktion 4.0, das drei Prinzipien folgt: smart, lean & green.
Dabei steht „smart“ für eine flexible, intelligent vernetzte Produktion durch den Einsatz neuer Technologien. So kommen unter anderem flächendeckend funkbasierte und akkubetriebene Schraubwerkzeuge zum Einsatz. Dank einer durchgängigen Vernetzung durch die Echtzeit-Ortung arbeiten diese bei jeder neuen Schraubposition mit dem passenden Drehmoment. Anstelle eines starr laufenden Fließbandes setzt Porsche für die Montage des Taycan als erster Automobilhersteller weltweit auf den Einsatz fahrerloser Transportsysteme. Diese bieten eine zuvor ungekannte Flexibilität im Arbeitsfluss, aber auch für die Architektur, die ohne aufwändige Fundamente mit doppelten Böden auskommt, schließlich benötigen die flexibel steuerbaren FTS lediglich ebene Flächen.
„Lean“ bedeutet eine möglichst effiziente Fabrikgestaltung, die Verschwendung und Handhabungsschritte auf ein Minimum reduziert. Schon die Werksplanung folgt dem Ansatz einer schlanken Produktion: So wurden für die Konzeption der Taycan-Fertigung digitale Planungsmethoden eingesetzt. Dadurch lassen sich die einzelnen Gewerke bereits im Vorfeld digital abbilden und der Betrieb sämtlicher Anlagen virtuell simulieren. Nicht zuletzt deshalb vergehen nach Messepremiere der Studie Mission E bis zur Eröffnung der Fabrik für den ersten Elektro-Porsche keine vier Jahre. Die neue Produktionsstätte entsteht parallel zu einer mit täglich 250 Fahrzeugen der Baureihen 718 und 911 voll ausgelasteten Fertigung am Porsche-Stammsitz.
Maßstäbe setzt die neue Produktion auch in Sachen Ressourceneffizienz und Nachhaltigkeit, dem dritten Grundprinzip der Porsche Produktion 4.0 – „green“. Für den Sportwagen-Hersteller ist es von vornherein erklärtes Ziel, mit dem ersten elektrischen Sportwagen der Marke Maßstäbe zu setzen, auch in puncto Umweltfreundlichkeit. Porsche folgt der Vision einer „Zero Impact Factory“, einer Produktion ohne Umweltauswirkungen. Dementsprechend ist es für die Marke selbstverständlich, das lokal emissionsfreie Fahrzeug auch CO₂-neutral zu produzieren
Im Mittelpunkt steht bei Porsche stets der Mensch. Und auch auf absehbare Zeit werden die hochindividuellen Fahrzeuge von Menschen für Menschen gebaut. Dabei unterstützen und entlasten moderne Technologien und digitale Assistenzsysteme die Kollegen bei der täglichen Arbeit. Dazu zählen auch Mensch-Roboter-Kooperationen, bei denen die Mitarbeiter durch Roboter unterstützt und ergonomisch entlastet werden.
Auch in der Lackiererei und Montage wird das Thema Ergonomie großgeschrieben, wie mit den um 110 Grad drehbaren und stufenlos höhenverstellbaren Fahrzeug-Gehängen oder elektronischen Wagenbegleitkarten, die Mitarbeiter über Bildschirme am Fahrzeug fortwährend über Ausstattungsdetails und Arbeitsschritte informieren.
Ein attraktives Arbeitsumfeld fördert die Potenziale und Kreativität der Mitarbeiter und leistet damit ebenfalls einen maßgeblichen Beitrag für die Porsche-typische Qualität.
Gestaltungsprinzipien der Porsche Produktion 4.0
- KI-gestützte Entscheidungen
- Wandlungsfähige Prozesse und Strukturen
- Situativ anpassungsfähige Fabriksteuerung
- Flexibler Mitarbeitereinsatz
- Assistierte und ergonomische Arbeitsplätze
- Vernetzte, kommunizierende Produktionsmittel und Produkte
- Ressourcenschonende Prozesse und Technologien
- Shopfl oornahe Problemlösungen
- Proaktive Qualifi zierung und aktive Regeneration
- Für Kunden transparent, live und erlebbar