The beginnings
The first Porsche 356 produced in Stuttgart leaves the plant in Zuffenhausen on April 6, 1950. Already the following year, the one thousandth of the sports car with a sheet steel body is produced. The first 52 examples were made in Austria in 1948 and 1949 - by hand and with an aluminum bodywork. Originally Ferry Porsche and his team thought of a series of 500 vehicles. In fact, until the end of production in 1965 about 78,000 Porsche 356 were put on wheels.
In the mid-fifties, the company has around 500 employees, who produce eleven 356 a day. The bodies come from the neighboring company Reutter. Porsche production and engine construction are housed in the Sheddach-Halle, which today is the heart of the area designated as Plant 2. The production is located in the vicinity of the brick building known as Plant 1, built in 1938, and which at that time was used by both the management and the design department. With increasing production figures, the plant is undergoing appropriate adjustments. But body shop, paint shop, engine assembly, saddlery and final assembly are still in spatial proximity.
Growth with the 911
The 911 is successfully following in the footsteps of the 356. Global demand is increasing, requiring several factory extensions. And the spatial conditions in the growing Stuttgart district of Zuffenhausen call for new solutions: Building 41 is in 1969 the site of a multi-storey production building. Engine construction has already been outsourced to a separate, south-facing building, and Plant 2 has been expanded to include a further hall. The new assembly building makes it possible to spatially separate individual production areas. This creates space for optimizing the production flow and enables the increase of production capacities. Instead of the former 70 vehicles, around 90 sports cars can now be produced. In 1973 Porsche employs a good 4,000 people. The two-storey assembly is still in operation – in a constantly modified form. Among other things, Building 41 is extended and modernized in the late 1970s and mid-1980s. In the Schwieberdinger Street, the heart of the site, the two-door sports cars are produced today.
Expansion in Zuffenhausen
At the end of the eighties more than 8,000 people work for Porsche. The workplaces are distributed over the production in Zuffenhausen, the development department in Weissach and further offices in Ludwigsburg. In Zuffenhausen, an automated high-bay warehouse (1982), the once again extended assembly (1985) and a new paint shop (1986) were put into operation. In the paint shop built on the grounds of Plant 2, fully automated transport systems and – for the application of PVC underbody protection – painting robots are used. Just in time for the start of the 911 Generation Type 964, in 1988, a new body shop is added in the immediate vicinity of the Plant 1. The freshly produced bodies reach the paint shop by means of a connecting conveyor bridge – relieving the heavy traffic on the site.
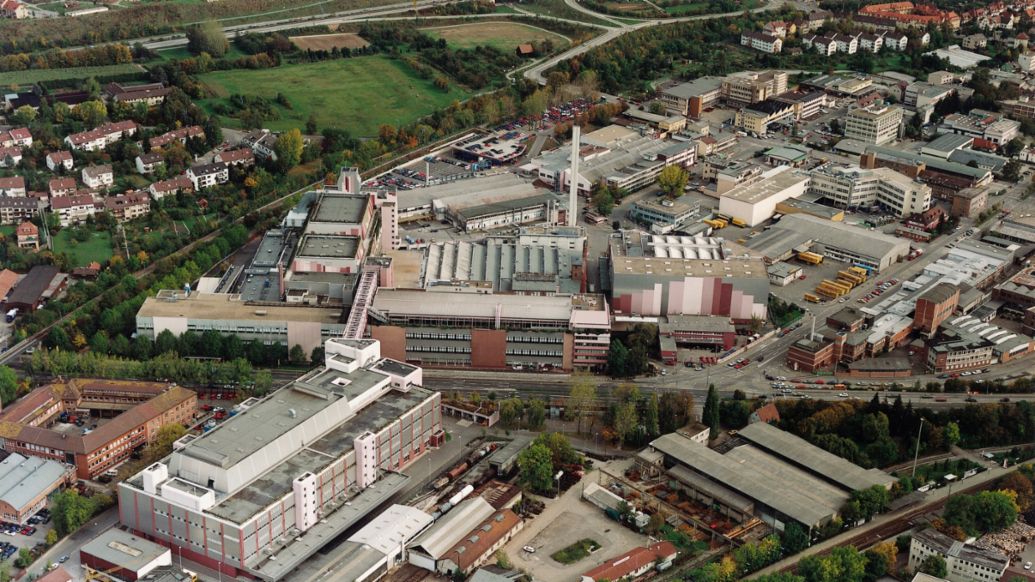
The factory of the future
The premiere of Porsche's first all-electric sports car is also accompanied by major changes to the traditional location. The urban location makes the spatial distribution of the various lines of work across the entire company premises necessary. For example, the new body shop, located at the heart of the site, will be joined by the buildings erected to the west for the electric drive and component production as well as a new paint shop. In the northeast is the Building 70 a multistory assembly. The painted bodies and drive components reach the assembly building by means of a 900-meter connecting conveyor bridge – unaffected by weather and without impairing public transport. The loading logistics for the finished Taycan are located east of the Building 70.
Porsche pays the highest attention to sustainability in all its aspects. Production on the site is CO₂-neutral, the energy-efficient buildings are well below the statutory energy requirements, all roofs of the new buildings are landscaped and partly equipped with photovoltaic systems. Biogas-powered combined heat and power plants supply the site with heat and additional electricity. Increasingly electrified logistics vehicles and rail transport powered by green electricity reduce CO₂ emissions in logistics. Added to this there are a host of other measures, with which Porsche is pursuing the goal of the "Zero-Impact-Factory", a production without environmental influences.
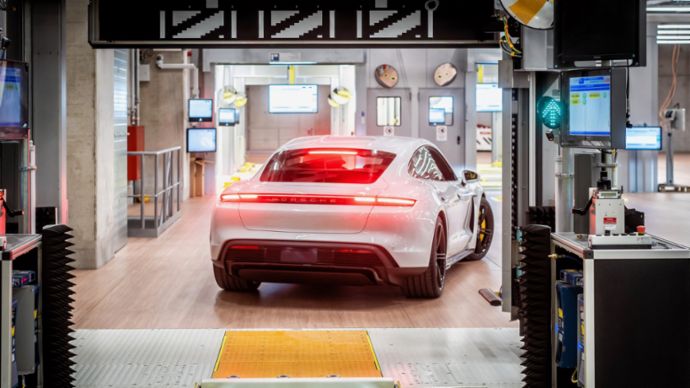