Before the new Porsche Cayenne was presented in April last year, the prototype had already driven four million test kilometers. But that was just the trips on real roads and off-road terrain—not including the virtual test drives in simulation. Nowadays, more than 1,000 kilometers are driven on the computer for every real-life test kilometer. The engineers generate a digital twin of the vehicle and then put it through its paces in virtual test drives in a simulation environment on a synthetic or hybrid test bench (SiL, HiL, ViL)—primarily in situations that rarely occur in real life or are too dangerous to test in real conditions. How does the cruise control react, for example, when there’s a wild boar waiting at the end of a curve?
For the validation of driver assistance systems and highly automated driving functions, it becomes indispensable to test such so-called 'corner cases' in countless variants and different levels of criticality. This, in turn, makes another resource increasingly important: virtual roads and environments.
“Every function that needs to be validated by a simulation requires a route model—a digital twin of the road and environment,” explains Tille Karoline Rupp, Senior Manager Simulation at Porsche Engineering. In the past, such scenes or track models were often generated manually, but that method is insufficient to meet the rising demand— after all, many billions of test kilometers will have to be driven on the way to the autonomous car. “A high degree of automation is crucial,” says Rupp. Porsche Engineering has developed its own end-to-end tool chain to generate virtual test tracks from a range of raw data—almost entirely without manual intervention.
One example of source material for scene generation is high-resolution maps from suppliers or real test drives that Porsche Engineering itself carries out with its JUPITER (Joint User Personalized Integrated Testing and Engineering Resource) test vehicles. Map data from public services such as Google Maps are not suitable for scene generation or track modeling. “We sometimes go down to the millimeter level and need information about lane and road width as well as three-dimensional cross-slopes,” says Tobias Watzl, Development Engineer and responsible for track modeling. Because the data basis differs from country to country, a local presence is sometimes critical. In China, for example, special legal requirements apply to the collection of geo-referenced road data. Thanks to its teams in Shanghai and Beijing, Porsche Engineering can assume responsibility for individual project scopes on site—always in cooperation with the experts from other locations.
Step-by-step Construction of the Track Model
In the first step, a logical model of the road is derived from the map data. It describes its course according to road construction guidelines using mathematical functions—mostly polynomial equations. The logical road model is stored as an Asam OpenDRIVE® file—a format that is managed and updated by the standardization organization Asam e.V. (Association for Standardization of Automation and Measuring Systems).
“We sometimes go down to the millimeter level and need information about lane and road width as well as three-dimensional cross-slopes.” Tobias Watzl, Development Engineer at Porsche Engineering
In the second step, a three-dimensional model of the road is generated—this being a visual representation that can not only be viewed on the screen, but can also interact with sensor models. This virtual test track can be changed in any way required, adding slip roads or infinite circuits. Generic scenes with no real-life counterpart are also adapted to the driving function to be tested. If the objective is an algorithm for traffic sign recognition, for example, numerous different signs are placed along the road.
Alternatively, the engineers can also model real roads— such as the A8 freeway from Stuttgart to Munich. Such georeferenced scenes are required, for example, if the function to be tested uses an internal map. Initially, the 3D model represents the road only. However, in order to be able to optimize camera-based functions such as lane detection, the virtual track model must look like it does in reality. To do this, it is given a virtual environment. For this purpose, Porsche Engineering has integrated the 3D graphics software Houdini into its pipeline, which is also used in the film industry. This allows for generate realistic-looking trees or buildings along the road. The information about where which objects are located along the road is extracted from sources such as the open map service OpenStreetMap (OSM).
However, modeling a photorealistic digital road and its environment is very time-consuming. “If all the input data is correct, an hour of computing time is required for about ten kilometers,” Watzl says. This requires a balancing act by engineers: The track model needs enough details to be able to reliably validate the respective driving function, however can’t be too large or it is likely to require too much computing power. To ensure that the simulation ultimately runs smoothly, distant or irrelevant objects are removed or modeled in a highly simplified form.
Automated Tool Chain
The highest possible degree of automation is crucial for efficient track modeling. The international team from Porsche Engineering has therefore developed its own end-to-end tool chain: All steps from the logical road descriptions to the finished 3D model with environment run automatically. This requires a wealth of digital intelligence: Assuming that the logical road model does not exhibit any inclination, but 70 meters are documented in the ground elevation data, the algorithm has to recognize that there is a tunnel at this point and add the matching tunnel to the 3D model.
“We need jointly defined quality requirements in order to be able to combine the best available tools in a reliable tool chain.” Marcel Langer, Product Owner for Simulation and Testing at Cariad
Moreover, quality assurance and using the data in various simulation environments without major modifications are also key elements. “We verify the data semantically with regard to drivability, importability and compliance with the standard,” emphasizes Rupp. For example, jumps in the road geometry that may occur due to measurement errors must be identified automatically. In addition to drivability testing in the respective simulation environments, a quality checker tool from Cariad is used. It checks whether an Asam OpenDRIVE® file is standard-compliant and can be used without limitations in the desired simulation environment.
Together with Cariad and Asam, Porsche Engineering has launched an initiative that aims to enable the interchangeability of standards and the ability to assess their quality. In the resulting Asam Quality Checker project, a review framework will be developed in 2024 together with other project partners as an important basis for improving the interchangeability of standards. “Scalable simulation solutions can only exist with standards that are interpreted and implemented uniformly,” emphasize Marius Dupuis, CEO of Asam, and CTO Ben Engel. “Without standards, the world is indescribable.” This assessment is confirmed by users: “In addition to the standards, we need jointly defined quality requirements in order to be able to combine the best available tools to develop or set-up a reliable tool chain,” says Marcel Langer, Product Owner Simulation and Testing at Cariad. When it comes to adapting the model to the simulation environment, Porsche Engineering can play to its strengths.
“We know the requirements for the simulations inside and out because we develop them ourselves and use them successfully in customer projects,” as Rupp underscores. One example is hardware-in-the-loop systems, which make it possible to test the function of a real control unit in a virtual vehicle with the corresponding environment and surrounding traffic. This reduces the need for real tests. Porsche Engineering employs a high number of such HiL systems.
Advancing with Weather and AI
As we proceed towards highly automated driving, virtual test tracks will need to become more extensive and detailed in the future. “There is still a lot of potential,” says Watzl. Here’s an example: At the moment, it’s always summer in the virtual world—the roads are clean and dry. “In the future, a winter variant could be introduced, with piles of snow on the side of the road that cover lane markings,” says Watzl. What’s important is that not only piles of snow, but also, for example, piles of leaves or puddles are displayed visually. In addition, their physical properties must also be reproduced correctly.
After all, there is a crucial difference between optical and physical detection of of the sensors—and thus also a difference in how the driver assistance systems will react. To further increase the level of detail, Porsche Engineering is planning to apply its internal expertise in artificial intelligence. “AI can automatically analyze satellite images and provide information about the landscape or buildings,” says Rupp by way of example. In addition, the technology can be used to automatically extract elements such as trafficsigns from video recordings. This could significantly accelerate the adaptation of a route model to another country.
From real to realistic
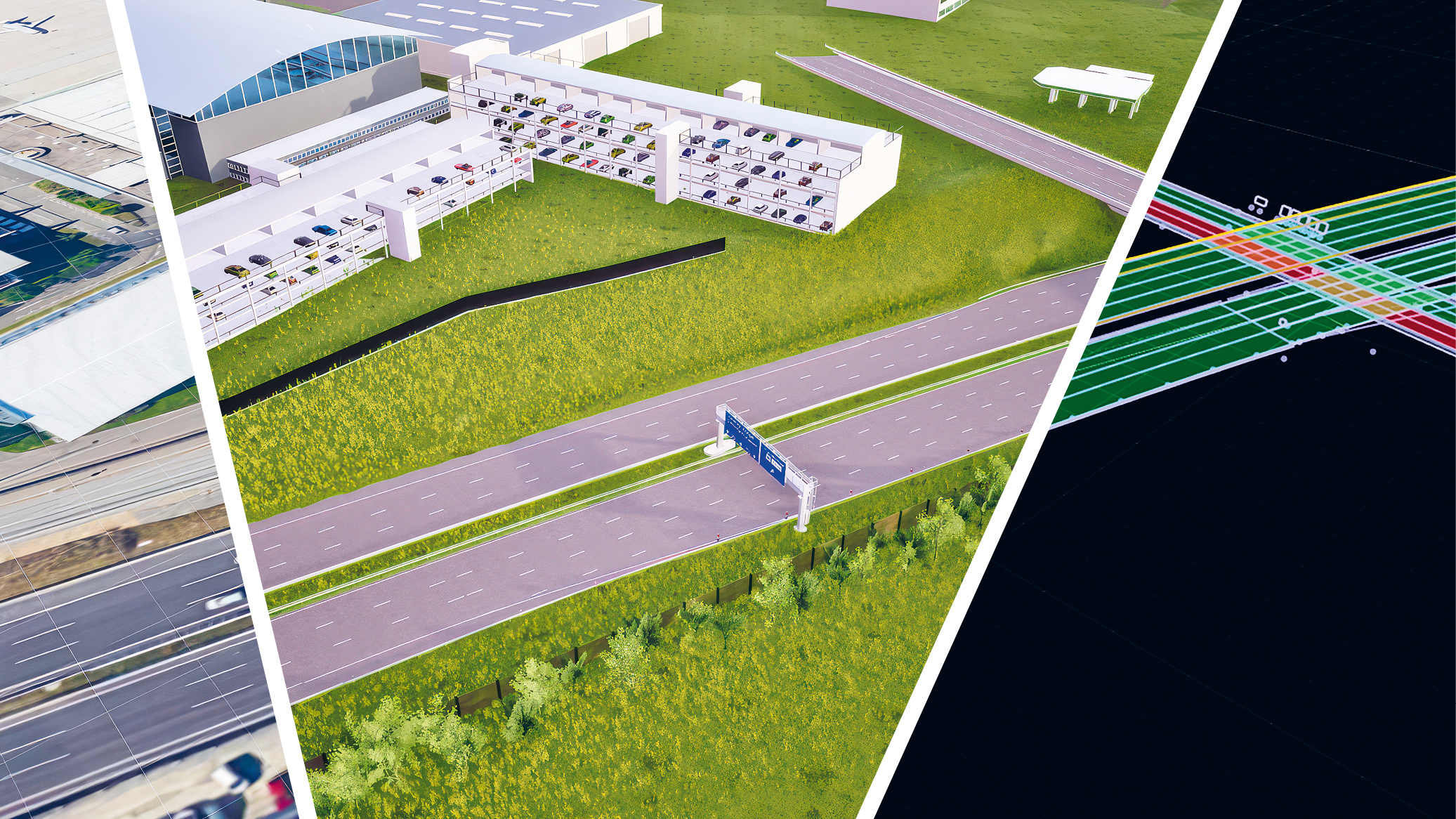
Two components of scene generation: Scene generation is a depiction of a scenario that usually exists in reality (aerial view at left). It consists of two components that match each other in terms of geometry and content: firstly, a logical-mathematical description of the road network and objects (right) and a 3D model of the drivable area and surroundings (centre). Scene generation is an essential component for virtual validation and development-supporting testing on synthetic and hybrid test benches (SiL, HiL, ViL).
Info
Text first published in the Porsche Engineering Magazine, issue 1/2024.
Text: Constantin Gillies
Copyright: All images, videos and audio files published in this article are subject to copyright. Reproduction in whole or in part is not permitted without the written consent of Dr. Ing. h.c. F. Porsche AG. Please contact newsroom@porsche.com for further information.