”We achieved a record result in 2021 in spite of all the challenges. This shows how efficient the Porsche family is. Many thanks for the passion, professionalism and team spirit.“ Albrecht Reimold, Member of the Executive Board – Production and Logistics
2021 was another year full of challenges. Total production was 300,081 vehicles, which corresponds to an increase of 14 per cent compared with the previous year. For the first time, vehicle production at both sites was entirely balance-sheet CO₂-neutral as the Leipzig site followed in the footsteps of the main plant, which had already switched to balance-sheet CO₂-neutral production in 2020. A total of 38,474 Taycan vehicles were manufactured in Stuttgart-Zuffenhausen. Additionally, all the vehicles of the 911 (38,790 units), 718 Boxster (11,726 units) and 718 Cayman (6,751 units) model series rolled off the production line at the main plant.
At the Leipzig plant, the company produced a total of 118,107 vehicles, which equates to more than one third of Porsche’s total production. There were 84,857 units of the Macan model series and 33,250 Panamera produced in Saxony.
At the Volkswagen Group’s multi-brand site in Bratislava, Slovakia, 86,233 units of the Cayenne model series were produced.
Production volume – Vehicles
2019 | 274,463 | |
2020 | 263,236 | |
2021 | 300,081 |
Successful crisis management
The coronavirus pandemic remained the primary challenge in the year under review. In addition, a global shortage of semiconductor capacities presented the company with some major difficulties, with creative solutions being called for in particular in the Production department. Together with the Volkswagen Group’s task force and all of the Porsche Group departments, a real effort was successfully made to minimise the impacts. Our vehicle models’ production planning was optimised and managed in such a way that the Zuffenhausen and Leipzig plants only had to temporarily reduce their production. Additionally, in the first half of the year in particular, operation of the Volkswagen plant in Bratislava had to be modified only to a minor degree.
Early communication with our partners and suppliers was important. Daily conference calls were held, sometimes involving more than 100 participants that included finance specialists, logisticians and procurement experts. Porsche continuously consulted all the partners. The experience gathered and agility were used to rethink and redesign processes.
Smart press shop goes into production
The smart press shop, a joint venture of Schuler and Porsche, went into operation in mid-2021. The press shop in Halle is one of the most state-of-the-art and most innovative of its kind in the world. The aim is, in particular, to achieve even greater dovetailing of design, development, body planning, tool manufacture and production, and to make the logistics paths more efficient and, above all, balance-sheet CO₂-neutral. The smart press shop also expands the conventional business line of a press shop with the addition of what’s known as laser cutting technology. This innovative technology is an ideal solution for manufacturing small batches of aluminium body parts.
Assembly capacities in Malaysia
In Asia, Porsche has its sights set on value-creating growth. The company is therefore increasing its presence in South East Asia’s emerging markets – the first cross-border high-performance charging network is being developed together with Shell and the sports car manufacturer is also expanding its production network with the addition of a local assembly line in Malaysia. This was developed together with its long-term partner Sime Darby Berhad and expands Porsche’s European production network. From 2022, Cayenne models which are specially and exclusively tailored to the Malaysian market will be produced in the Kulim District. A partnership has now existed with Sime Darby for 10 years. The company is an importer and dealer for Porsche in Malaysia. As a founding member of ASEAN, Malaysia offers good business and development opportunities.
The island country also has a well-developed and established automotive industry.
Production in Zuffenhausen
At the main plant in Zuffenhausen, an average of more than 400 vehicles rolled off the production line every day – more than ever before in spite of the semiconductor shortages. A sophisticated control and production principle allows the assembly of all twodoor sports cars – the 911, 718 Boxster and 718 Cayman model series – on one production line. Highly individual customer wishes can be integrated directly into series production thanks to the flexible production system. Put simply, no two vehicles are exactly the same. This also applies to the Taycan, which is produced in its own factory within the factory – without a conventional assembly line.
At the Taycan paint shop, the bodywork holes needed for corrosion protection are now sealed much more effectively. The previous plastic plugs have been replaced by sticky pads.
New production process at the Taycan paint shop
Porsche has developed a new production process in Zuffenhausen in cooperation with Tesa SE – at the Taycan paint shop, the bodywork holes needed for corrosion protection are now sealed much more effectively; these holes are needed so that the paint shop can reach all the hollow spaces. The innovative solution involves the plastic plugs previously used being replaced with sticky pads. The all-electric Taycan is the first vehicle in the world to feature this new process. A robot automatically, quickly and reliably positions more than 100 sticky pads and seals the bodywork holes, thereby optimising the efficiency of Porsche production. The paint shop at the plant in Leipzig was likewise transitioned to this innovative process in the year under review.
Near-natural company grounds at the main site in Zuffenhausen
On the occasion of World Environment Day on 5 June 2021, Porsche presented the first section of land on its way to making the company grounds at the main site in Zuffenhausen near-natural. Approximately 2,000 square metres of space which was previously occupied by the plant’s vehicle sales was environmentally upgraded. The new green and blooming environment offers the main plant’s neighbours natural noise control. At the same time, the company is voluntarily opening this space up to the public – the area serves the neighbours as recreational space and offers the employees better sojourn quality.
At its site in Leipzig, Saxony, Porsche has been applying a unique grazing concept across its 132-hectare off-road site since 2002. With its specially created ponds, wetlands and grazing land, the site offers a natural habitat for numerous types of flora and fauna.
The Porsche site in Leipzig is shaping up for electromobility. The decision to produce the next generation of the Macan as an all-electric variant in Leipzig means that Porsche is investing around 600 million euros in the site in Saxony.
Production in Leipzig
Around 550 vehicles from the Macan and Panamera model series were produced on a daily basis at the Porsche plant in Leipzig. Meanwhile, the site is also shaping up for electromobility. The decision to produce the next generation of the Macan as an all-electric variant in Leipzig means that Porsche is investing around 600 million euros in the site in Saxony. With this latest plant expansion, the company is creating the possibility of producing fully electric vehicles on the existing production line alongside petrol and hybrid models in future. In addition, another important step was taken in the direction of a smart factory in 2021 – a private 5G research network was put into operation together with Ericsson. The first of its kind in the Porsche production environment, it will pave the way technologically for the factory of the future. The 5G network creates the basis for the instantaneous and secure transfer of data between people, machines and vehicles.
Porsche Leipzig expands its training centre
The Leipzig site opened the extension of its training and qualification centre right on time for the start of the new training year. The 1,600-square-metre extension directly adjacent to the existing building comprises training and communal rooms. Vocational training has grown together with the Porsche factory – when the first Porsche Cayenne rolled off the production line in 2002, there were five trainees at the site; there are now more than 120. The training centre built in 2017 has been extended in order to adapt the training to the ever-changing conditions in the automotive industry. This will result in some significant advantages. Until now, the training workshop for industrial mechanics and mechatronics engineers was located in Assembly. Thanks to the extension, all the apprenticeship trades are now together under one roof. The new premises also offer space for the qualification and further training of employees with career experience. Training with robots and CNC machines can therefore be expanded.
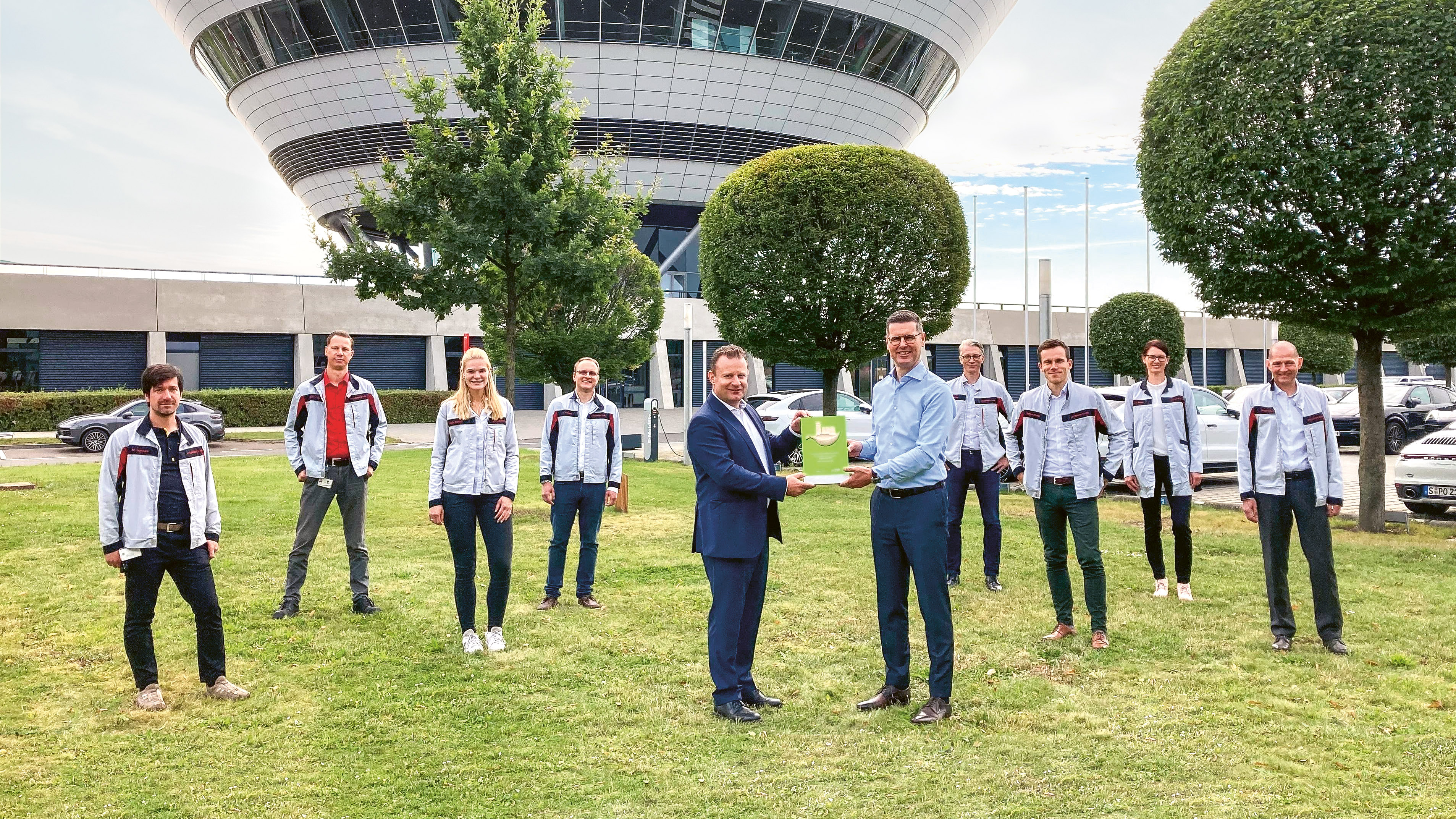
The Porsche plant in Leipzig received a Lean & Green Management Award in 2021. The competition recognises the most successful lean management approaches together with environmental and sustainability aspects.
Lean & Green Management Award 2021 for the Leipzig plant
The Porsche plant in Leipzig received a Lean & Green Management Award in the category Automotive OEM in 2021. The jury awarded the Porsche site in Saxony the distinction Lean & Green World Class. The competition recognises the most successful lean management approaches together with environmental and sustainability aspects.Two hundred and fifty plants from more than 10 countries and 20 industries entered. The Leipzig plant made an impression first and foremost with the Porsche improvement process, which is firmly embedded in the production system, and with its resource efficiency programme. The processes are regularly scrutinised in environmental and energy audits in order to achieve continuous improvement. From 2014 to 2020, resources worth just under 3.5 million euros were saved thanks to the implementation of such measures. With the Leipzig factory’s own “Environmental impact reduction in Production” performance indicator, the plant serves as a benchmark for the automotive industry. The plant also scored points for its high degree of transparency regarding the consumption of resources and its needs-based control, for example in the area of lighting.