Vehicles and their control systems are becoming more and more complex, while the number of available prototype vehicles continues to decline. Developers are therefore increasingly relying on virtual and hybrid tests using advanced simulation methods such as Software in the Loop, Model in the Loop, Hardware in the Loop and other methods, with the goal of tackling testing activities as early as possible in the development process. These simulations have long since become the standard for the objective evaluation of vehicle components, mechanical systems, and driving functions. However, they do not allow any human interaction or subjective assessment. This is where tests with driving simulators come into play—because they also include the human perspective.
“By combining driving simulators with HiL systems as well as the consistent use and continuous expansion of the specially developed simulation framework on the driving simulator, we can obtain subjective feedback on new digital functions early in the development process—long before the first prototypes are available for this,” explains Tille Karoline Rupp, Senior Manager Simulation at Porsche Engineering. “This ‘frontloading’ means that the functions are much more sophisticated when they are first used in a test vehicle later on.” Moreover, tests with driving simulators are a cost-effective supplement to real-world testing. They not only make it possible to carry out risky tests in a safe environment, but also allow tests to be implemented under widely varying weather conditions on virtual test tracks that are ideally adapted to the respective problem.
Another advantage is that the test situations are exactly reproducible. For example, the surrounding traffic can be specified precisely and repeated at will, which is all but impossible in reality. In one current project, the developers are using driving simulators to apply the parameters of the brake control system software to specific vehicle types.
Porsche Stability Management (PSM), also known as the Electronic Stability Program (ESP), consists of two main components: The anti-lock braking system (ABS) and the vehicle controller. The ABS can regulate the hydraulic pressure on the individual wheel brakes when the driver applies the brakes. If there is a risk of instability in a corner, individual wheels are braked to prevent skidding. “The brakes behave very differently depending on how damp it is and the temperature, as well as the condition of the road surface and brake pad,” says Martin Reichenecker, Senior Manager Driving Dynamics & Validation at Porsche Engineering. “The ESP has to compensate for these fluctuations—as well as the difference between summer and winter tires.” The software for the ESP control unit comes from tier-1 suppliers and is delivered with a set of standard parameters.
These parameters must be optimally matched to the different vehicle variants by the developers over the course of the calibration process. The challenge: Test vehicles with sufficient component maturity are not yet available for this purpose in the early stages of the development process. Porsche Engineering therefore wants to increase its use of driving simulators for the subjective assessment of ESP functions. “To do this, we employ comprehensive integration of vehicle and scene generation, a real control unit with associated software, and a user interface that allows the driver to interact directly using the steering wheel and pedals,” reports Reichenecker. “This allows us to carry out the journey in real time under the most realistic conditions possible.”
Authentic driving experience
The realistic simulation of driving physics in real time, in combination with a suitable virtual test track, guarantees an authentic driving experience in the driving simulator. The driver feels the steering wheel torque and in the virtual test drive on the simulator experiences whether the vehicle spins out, for example, when braking. Using the insights gained in this manner, developers can start calibrating the ESP function for a specific vehicle at an early stage, which significantly shortens the development time. Rupp, Reichenecker, and their colleagues have been working on the new method for around a year. The frontloading has performed as expected; the first test drives for the ESP application are planned for the end of 2024 or early 2025.

The developers have already completed a virtual testing ground that can be used to test all track sections that are relevant for ESP development with different friction coefficients and weather conditions in a single environment. The use of driving simulators for calibration is facilitated by several of Porsche Engineering’s distinctive capabilities. For example, developers can generate any given virtual track model (see Porsche Engineering Magazine 1/2024), for example with hot or icy roads, in the lowlands or in the mountains. With the help of the findings from the AVEAS research project (AVEAS is a German acronym meaning ‘collecting, analyzing, simulating traffic situations relevant to validation’) funded by the German Federal Ministry for Economic Affairs and Climate Action, in which Porsche Engineering plays a major role alongside a further 20 partners, it is also possible to identify critical situations during real test drives and apply them to the simulation.
The track models and traffic situations generated in this way are also varied in order to generate more test cases for virtual validation. “We bring our full range of modeling activities to bear and are thus able to offer customer-specific solutions—including the physics and visualization of the entire vehicle model as well as all roads and scenarios,” says Rupp. “This makes it possible to drive through Europe with all its different climates and terrain profiles in a short time in the driving simulator.” Porsche Engineering currently operates four static real-time driving simulators and two game-based driving simulators in China, Italy (Nardò Technical Center), Czechia and Germany.
All sites work together in their deployment and on further development, for example in the area of scene generation, the further development of the simulation framework, model integration, and the HiL connection. One of the game-based driving simulators is used to prepare developers for test drives.
Porsche AG has also been using driving simulators for years. Among other applications, they are used in the fields of vehicle functions, HMI (human machine interface), ergonomics, and driving comfort. “We use driving simulators primarily in studies with test subjects in which team members, test subjects or decision- makers are asked to evaluate, for example, new driving functions” explains Ingo Krems, Senior Project Manager of the newly established Virtual Validation Center (VVC) at Porsche.
“As part of the virtual complete vehicle test, participants can validate, experience, and evaluate the display and control elements, ADAS functions, ergonomics, and driving comfort of new vehicles.” Feedback from the test subjects flows directly into the further development of the new vehicles.
Porsche AG in Weissach is currently operating a driving simulator with a motion platform and high-end visualization system in series vehicle development as well as several small static simulators (including ones with VR glasses) to make it possible to experience vehicles virtually. This infrastructure is currently being further expanded as part of the VVC project. “We will build two additional driving simulators with moving platforms,” says Krems. “The first, the VFP.NVH lab, will start operations at the end of this year. Its application focus will be on driving comfort and acoustics. The second will follow at the end of 2026, concurrently with the opening of the VVC. Thanks to its innovative motion system, this simulator makes it possible to cover driving conditions that are significantly more dynamic, as well as urban driving situations, better than was previously possible.”
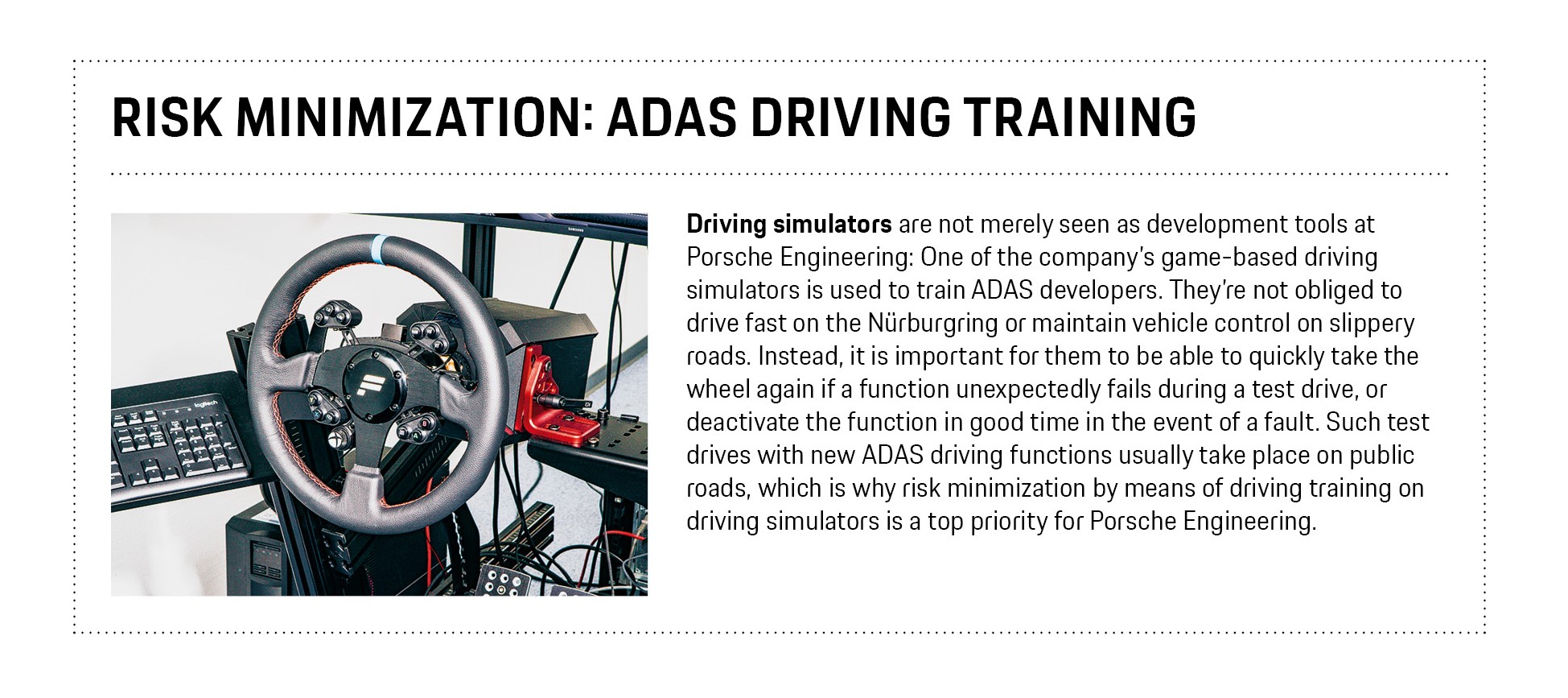
Virtual Validation Center in Weissach
The VVC is being built in the heart of the Weissach Development Center and will have a total area of 2,100 square meters. All large-scale simulators used in series vehicle development will be bundled in a building complex at the new location. New mini simulators are also being developed there to help prepare for, and make more effective use of, precious test time in simulators with motion systems. The center will be built in an existing building.
“We decided against a new building in order to avoid CO₂ emissions through sustainable construction and to use the valuable space in the development center efficiently,” reports Krems. “In keeping with the ‘modernity meets tradition’ concept, the new technology will be installed in one of the oldest buildings at the Development Center.” Porsche Engineering and Porsche AG use the same driving simulator framework for development. “This creates promising opportunities for cooperation between the two companies,” says Rupp. “For example, we could generate the required model set-up with the virtual roads, the surrounding traffic, the complete vehicle, and the driving dynamics and carry out integrated initial tests with our own static driving simulators. Based on these results, the developers could later seamlessly switch to Porsche’s moving driving simulators in order to immediately experience the dynamic behavior of new functions. In addition, extended tests in seating bucks with real ergonomics would be possible as a way of gaining insights into even more realistic prototypes.”
Reichenecker adds: “With our static driving simulators, we can carry out most of the calibration in a quick and lean manner, and with the dynamic driving simulations in the VVC we come very close to the real prototypes.”
Many areas of development should benefit from driving simulators in the future. “In addition to SiL and HiL tests, we see the driving simulators as a development- supporting, additional ‘tool’ in our toolbox—but not a substitute for the existing methods,” concludes Rupp. “Thanks to our expertise in scene generation and vehicle simulation, as well as taking into account the surrounding traffic and realistic interactions, we offer our customers modular solutions that can be optimally adapted to the respective application.”
Info
Text first published in the Porsche Engineering Magazine, issue 2/2024.
Text: Christian Buck
Copyright: All images, videos and audio files published in this article are subject to copyright. Reproduction in whole or in part is not permitted without the written consent of Dr. Ing. h.c. F. Porsche AG. Please contact newsroom@porsche.com for further information.