Upgrading the equipment in a Porsche and easily adding optional functions via software—this is possible thanks to the digital services of Porsche Connect. This gives drivers access to a wealth of additional functions that support them before, during, and after their journey. For example, if drivers so choose, they can easily add active lane guidance for even safer driving or an intelligent management function that adjusts the climate and speed settings to the electric vehicle’s remaining range. To ensure that the features are integrated smoothly into the vehicle system and that the many different services work seamlessly together, an international test team of around 110 employees at Porsche Engineering verifies the software for all Porsche model lines and individual models before it enters the vehicle.
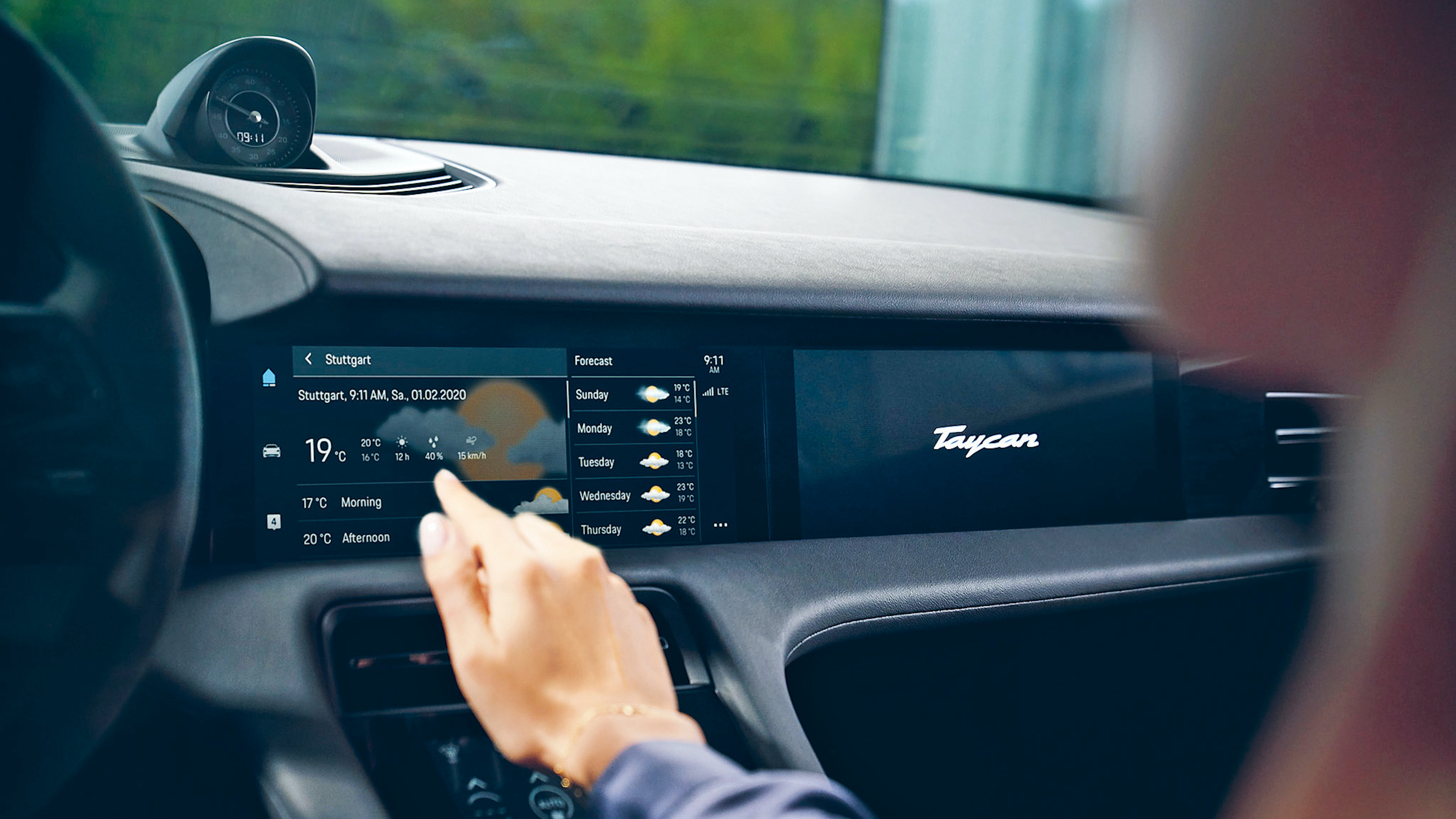
“The ecosystem formed by modern connectivity solutions such as Porsche Connect is particularly complex, as different software worlds— automotive, infrastructure, and smartphone—are integrated. In addition, there is a wealth of individual software functions that must be tested in all combinations,” as Dr. Fabian Hinder, who is a specialist project engineer at Porsche Engineering, explains.
The test steps in the laboratory and on the road which the software must be put through are therefore just as extensive as you would expect. Porsche Engineering has set up 30 special HiL (hardware-in-the-loop) test benches at its locations in Shanghai, Cluj, Prague, Ostrava, and Weissach for bench testing of Porsche Connect services. Only the four core control units installed in the vehicle for the Porsche Connect services are integrated as hardware; the other vehicle systems are reproduced in a virtual real-time environment. “This residual bus simulation, as it is known, is primarily used to generate the communication data for the various bus systems, meaning that we can test the Porsche Connect services under realistic conditions on the test bench,” says Daniel Klauber, a development engineer at Porsche Engineering.
“The ecosystem formed by modern connectivity solutions is particularly complex, as different software worlds are integrated.” Dr. Fabian Hinder Specialist Project Engineer at Porsche Engineering
During the tests, it is examined whether the software reacts as specified to various situations generated by the simulation. “Based on the results of these basic functional tests, known as smoke tests, the experts at Porsche Engineering decide how the further test sequences should be structured,” explains Klauber. These examinations are conducted at different locations around the world to test market-specific functions.
Even though the residual bus simulation and the implementation of the HiL test have been largely automated for a long time, the preparation of the test bench before and the processing of the results after the test were largely conducted manually. For example, the test bench engineers had to manually select the latest Connect software from the data management system and load it onto the control units in the test environment.
Complete Automation
A new Porsche Engineering concept now ensures complete process automation of the test bench tests. Not only are the tests themselves being automated, so are the accompanying processes. The system manages the software for the Connect services independently, and also uploads it to the test control units. The control unit parameterization and the start, execution, and analysis of the bench tests are also automated.
“This reduces the test engineers’ workload and speeds up the tests, as there is no need to carry out manual tasks between the process steps. The time required for manual work to prepare the test benches is thus reduced by around 90 percent. The system also actively alerts the test team to critical test results. The team can therefore concentrate fully on error analysis,” says Hinder.
Interdisciplinary Team
In addition, extensive expert knowledge is no longer required for some activities on the test bench, as was the case, for example, for the manual update of new software to the test control units. “In the Connect environment, there is an extremely high variance due to the number of services, the number of vehicle model lines to be served, and the number of markets. In order to be able to cover these variants with tests when there are weekly software deliveries, it is imperative that the HiL test bench be fully automated,” says Carsten Weigt, Team Lead Shared Test & Integration at Porsche AG.
Full automation was implemented with in-house know-how by an interdisciplinary project team at Porsche Engineering. Experts from the areas of software development, process automation, test automation, residual bus simulation, and test infrastructure design worked together at various locations worldwide. Part of the teams’ work involved supplementing the existing building blocks with interfaces it had developed itself to allow a more far-reaching automation of the process chain.
“It is imperative that the HiL test bench be fully automated.” Carsten Weigt Team Lead Shared Test & Integration at Porsche AG
“To reduce complexity, we defined automatic routines that make it easier for us to trigger processes,” explains David Karimi, a development engineer at Porsche Engineering. The experts used in-house developments to compensate for any lack of full-automation building blocks.
This allowed, for example, a local client to be created for controlling the test benches, as well as what is known as a software crawler, which automatically downloads software from suppliers’ servers. Other examples include generic control logic and reporting tools for documenting all results of the individual automated process steps.
Modular Design
The methodology used to fully automate the test benches is also referred to as continuous integration. At its core, the methodology is based on the opensource software system Jenkins, which allows ongoing assembly of software components to form an application. “Porsche Connect services continue to be developed fast and dynamically. In order to be able to safeguard the new services and changes in good time—despite the pace of development— we have pushed ahead with the introduction of HiL automation. With continuous integration, we can now automatically download new control unit software, and flash and code the control units very efficiently,” explains Dickson Ng, Product Owner Automation Platform & Continuous Integration at Porsche AG.
With its modular design, the continuous integration methodology offers a high degree of flexibility for adaptations and extensions, because different modules can be integrated into a new overall process depending on the use case. “This makes our approach suitable for automating all bench tests for all domains,” says Hinder. “We have already received the first requests from other departments.” For the time being, however, the project team is focusing on integrating full automation into all Connect HiL test rigs from Porsche Engineering worldwide. Following the successful initial implementation, all other test rigs in Germany, China, and the Czech Republic are now to be retrofitted. It is planned that all HiL test rigs for Porsche Connect services will be in fully automated operation by the end of 2023.
Info
Text first published in the Porsche Engineering Magazine, issue 2/2023
Text: Richard Backhaus
Copyright: All images, videos and audio files published in this article are subject to copyright. Reproduction in whole or in part is not permitted without the written consent of Dr. Ing. h.c. F. Porsche AG. Please contact newsroom@porsche.com for further information.