Modern car bodies are made of a number of materials. In the past, automotive bodies-in-white were manufactured primarily from cold-worked sheet steel. While still used today, it is widely found alongside aluminum, which weighs less. This mix of materials, also referred to as multi material design, first and foremost pursues a reduction in weight: Lightweight design is the catchphrase. It saves fuel and enables a faster start. But there’s more to it yet. Together with other technical design features such as rear-axle steering and improved passenger cell stiffness, lightweight construction also improves stability and safety.
Let’s take a quick look back at how far we’ve come: The 2004 model of the 911, the type 997, still had a body made entirely of steel. Its successor model in 2011, the type 991, had an underbody and roof made of aluminum. The new type 992 sticks with the aluminum underbody but the engineers also cut the share of steel down to less than half—it now barely scratches 30 percent. At the same time, the amount of aluminum increased once more, taking lightweight construction another step further.
Power-to-weight ratio: the lower the better
It should be noted, however, that lightweight by no means needs to equate to lighter and ever lighter. The essential aspect is the ratio between mass and engine power, referred to as the power-to-weight ratio. Expressed in kg/kW, it is calculated by dividing mass by maximum drive output. The lower the value, the better. Another look at the 911’s history shows us that the sports car always pursued this trend. It’s a history of constantly dropping power-to-weight ratios.
The lower power-to-weight ratio in the new 911 is not solely due to its more powerful engine. Uncompromising lightweight design played a major part, too. “Lightweight construction lies in Porsche’s genetic heritage, we always had weight optimization right there at the top of our agenda,” says Jens Christlein, head of body structure engineering at Porsche AG.
“We always had weight optimization right there at the top of our agenda.” Jens Christlein, Porsche AG head of body structure engineering
Making the new 911’s side panels entirely from aluminum was a logical step, then. The side panels now weigh twelve kilograms less, with no loss of stability. Designing them was quite the challenge for everyone involved. Compared with steel, aluminum offers less favorable material properties. “It’s far more prone to tearing through tensile deformation. This means the components require much more intense engineering,” Christlein explains. Among the tools used during development, stamping simulations were found to be indispensable, allowing the engineers to check the material’s behavior.
Another aspect key to completing the project successfully was the close collaboration of all departments from design engineering to Porsche’s in-house toolmaking division: There were meetings once a week, with everyone working on honing the details until all design and quality requirements were met. In some cases, the specialists needed to find their way to the ideal, millimeter by cautious millimeter. “The art lies in taking the vastly emotive look of the new Porsche 911 and adding lightweight design to form a unit,” says Christlein. It took all of the engineers’ decades of experience—and true grit: From start to production maturity, the process took more than two years.
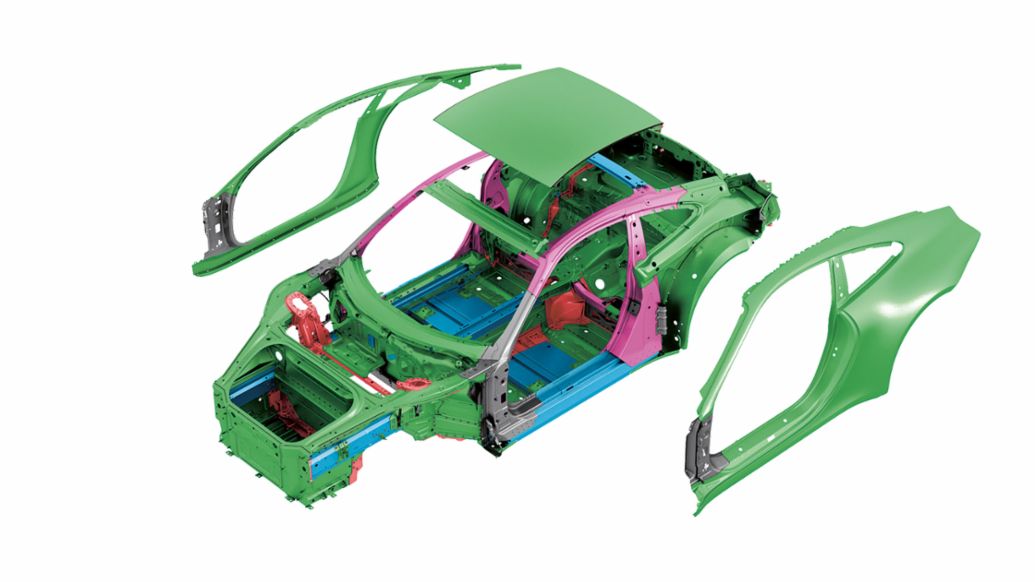
Beside the aluminum side panels, a range of additional innovative lightweight design techniques and methods are used for the new 911. Increased use of high-pressure die-cast parts, for example on the front spring strut mounts and rear tunnel housings, offers greater freedom in designing the body-in-white, because you can vary the parts’ geometry more easily. They also make it possible to combine multiple functions in a single component. Examples include integrated bolting lugs or reinforcement ribbing, which in classic sheet metal designs require multiple components— which both make production more difficult and add weight. The benefits gained from die-cast parts in the new 911 increase even further by using lightweight aluminum to make them.
The new 911 also uses a greater share of aluminum for its extruded profiles, for example in the front and rear side members. According to Christlein, “Geometry and boundary conditions permitting, extruded aluminum profiles are an excellent way to produce highly complex profiles at low tooling costs.” To meet the different requirements—load resistance being just one—the material is used at varying thickness.
Sustainable production: combining heat treatment and painting
Another innovation succeeds in making production of the 911 more sustainable. Heat treatment for the cast parts is now combined with the painting process. After casting, cast parts need to undergo heat treatment to acquire the desired material properties. “When they’re fresh from the mold, they don’t have the ductility we need, for example, which determines their deformation in a crash,” Christlein explains. This makes heat treatment the actual trick in producing cast parts. It also takes lots of time and energy. In manufacturing the new 911, Porsche puts the heat energy necessary for painting to double use by simultaneously using it to give the cast parts the required strength and ductility.
The growing number of different materials used in body-in-white production also increases the number of joining techniques. Hot-formed steel and aluminum provide a good example: Classic spot welding won’t work here, which is why friction welding is used instead. Friction welding works by pressing the rivet that will hold two sheets together onto the sheets against a bearing and then spinning it. The heat produced by the friction melts the rivet through the two sheets. Flow-drill screws follow a similar principle: They are driven into the material at high speed, producing heat that makes the material moldable. This way, the screw cuts a thread in which it can be tightened to join two materials.
The latest 911 body-in-white marks the model range’s best power-to-weight ratio so far. But the engineers refuse to rest there. They’re already considering new lightweight designs, including using materials like magnesium or carbon. In the end, however, adopting them will be a question of cost. But Christlein is adamant that lightweight construction can still be taken a good deal further: “We discuss the material mix in every new project, and arrive at a new conclusion every time, too.”
Info
Text: Jost Burger
Text first published in the Porsche Engineering Magazine, issue 01/2019