Lipski diament
Światowy poziom: Wiodąca technologia produkcji w wyjątkowym zbliżeniu.
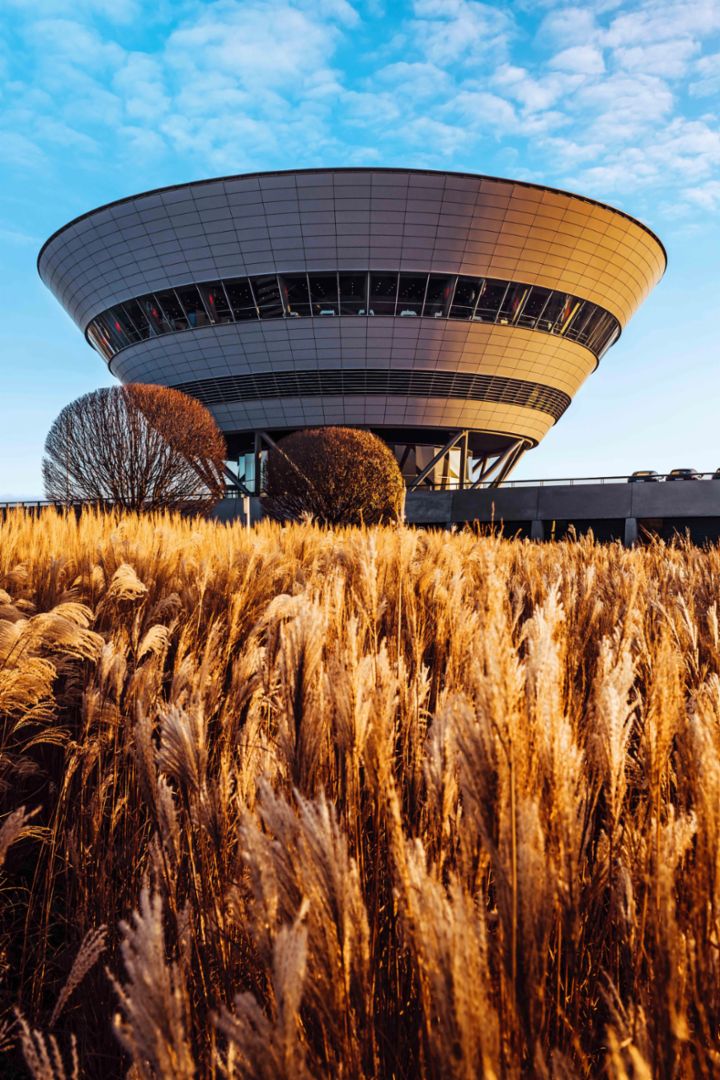
Budynek pnie się do góry na wysokość 32 m. Z oddali sprawia wrażenie lotniskowej wieży kontrolnej. Jednak większości ludzi stożkowa bryła przypomina oszlifowany diament. Stąd wzięło się określenie charakterystycznego obiektu w zakładzie Porsche. Jest nader trafne. Albowiem diament uosabia błyskotliwą historię sukcesu. Zaledwie dwa lata mijają od pierwszego wbicia szpadla w roku 2000 r. do uruchomienia produkcji Porsche Cayenne. Przedsięwzięcie związane z budową lipskiego zakładu toczy się w zawrotnym tempie i wiąże się ze sporym ryzykiem. Ale architektura świadczy o odwadze, a nie o obawach.
Równolegle do pierwszego SUV-a od 2003 r. produkuje się tu wóz sportowy Carrera GT – 1270 egzemplarzy składanych ręcznie. A ponieważ Cayenne jako samochód terenowy o wyjątkowo sportowym charakterze odnosi natychmiastowy sukces, już w 2004 r. zachodzi po raz pierwszy konieczność rozbudowy zakładu, co dotychczas miało miejsce pięciokrotnie. Modele Panamera i Macan przyczyniają się do kolejnych faz rozbudowy.
Ponadto do firmy zawitały napędy hybrydowe i elektryczne. O zakładzie w Lipsku zawsze myśleliśmy w kategoriach strategicznych, stale go rozwijając – mówi Albrecht Reimold, Dyrektor Produkcji Porsche i Przewodniczący Rady Doradczej Porsche Leipzig GmbH, spółki zależnej należącej w stu procentach do Porsche AG. „W przyszłości planujemy tam produkcję większej liczby modeli elektrycznych”.
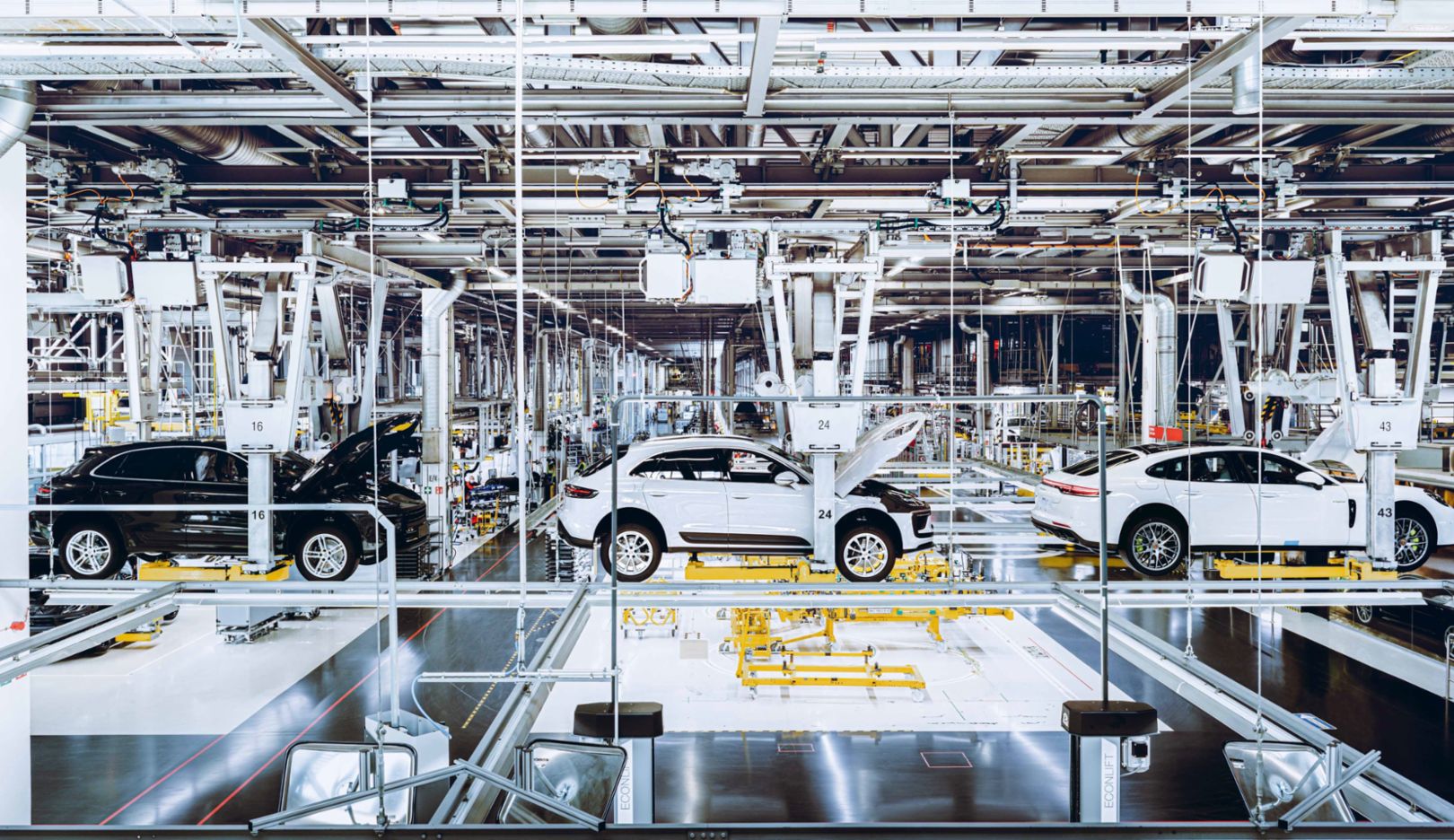
Produkcja mieszana:
In one of the world’s most cutting-edge assembly halls, all of the models pass through the same production line: Porsche Macan and Panamera, vehicles with internal combustion engines and hybrid powertrains, and soon even all-electric cars.Jeden zespół, jedna linia, trzy napędy – ta maksyma jest wszechobecna w ogromnych halach zakładowych. Na koszulkach, nalepkach, tablicach informacyjnych. Zgranie jest wzorowe, fluktuacja minimalna. 4300 ludzi produkuje dziś w Lipsku ponad 550 pojazdów – każdego dnia. „Nasz sukces”, mówi Gerd Rupp, „zawdzięczamy w dużej mierze naszej wysoko wykwalifikowanej i zmotywowanej załodze”. Kieruje zakładem jako prezes zarządu Porsche Leipzig GmbH, spółki zależnej w stu procentach od Porsche AG. Tysiąc ultranowoczesnych robotów wspomaga pracowników zwłaszcza w wykonywaniu prac wiążących się z dyskomfortem ergonomicznym.
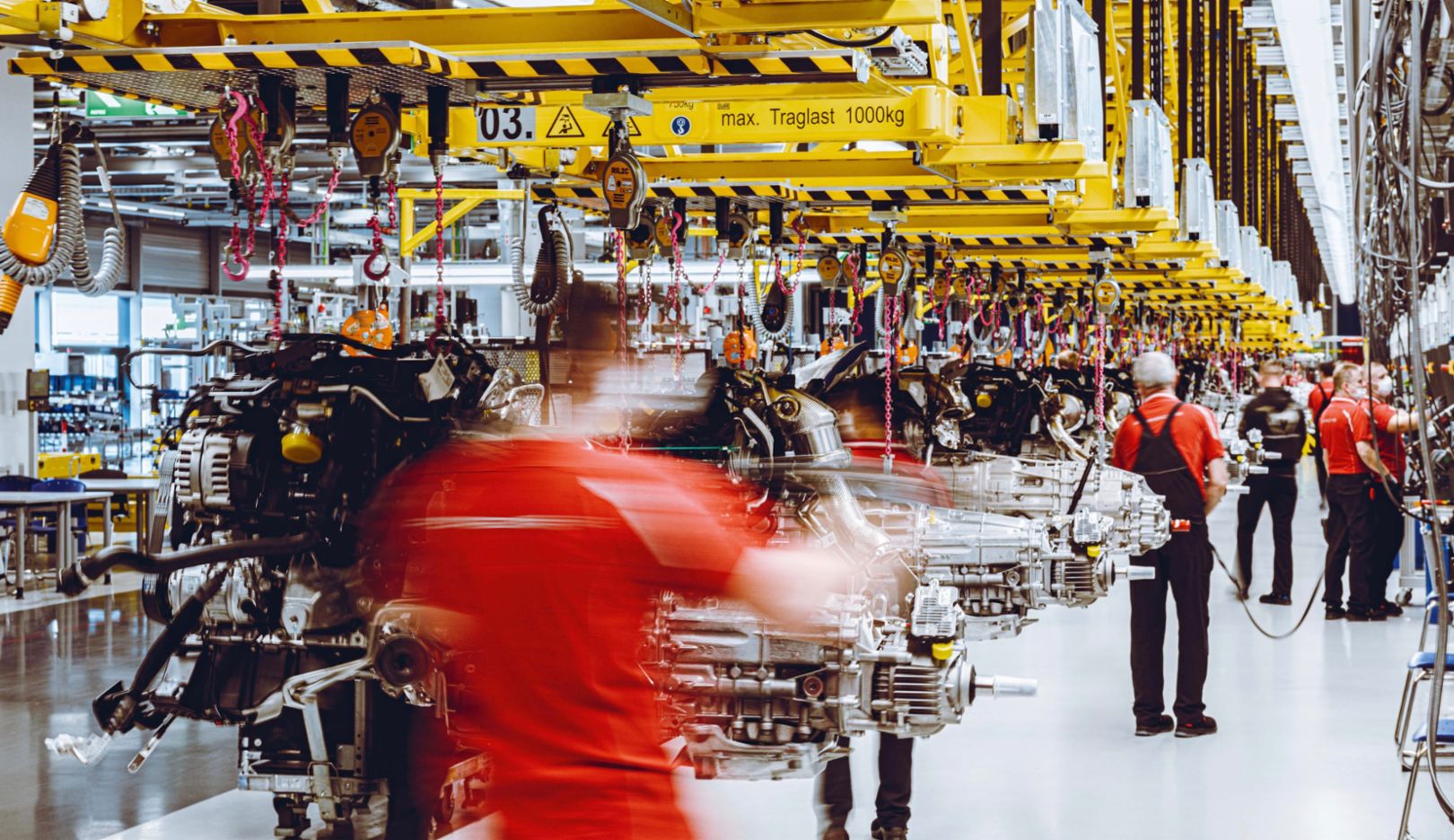
Kooperacja:
The Group manufactures the Macan and Panamera engines and delivers them to Leipzig. This picture shows engine preassembly and the upgraded chassis.Najmocniejszym punktem jest moduł 321, w pełni zautomatyzowany mariaż. Tu podwoza wyposażone zawczasu w układ przeniesienia napędu oraz karoserie łączą się w trwałym związku. Dzięki zmyślnej logistyce wszystkie komponenty zawsze trafiają na właściwe miejsce. Automatyczne pojazdy transportowe przemieszczają się po pasie indukcyjnym, dostarczając, czego potrzeba. Ci mali pomocnicy mają wyjątkowy udźwig i są arcypunktualni – a ponadto pieczołowicie dopracowani w słynnych projektach wyścigowych Porsche.
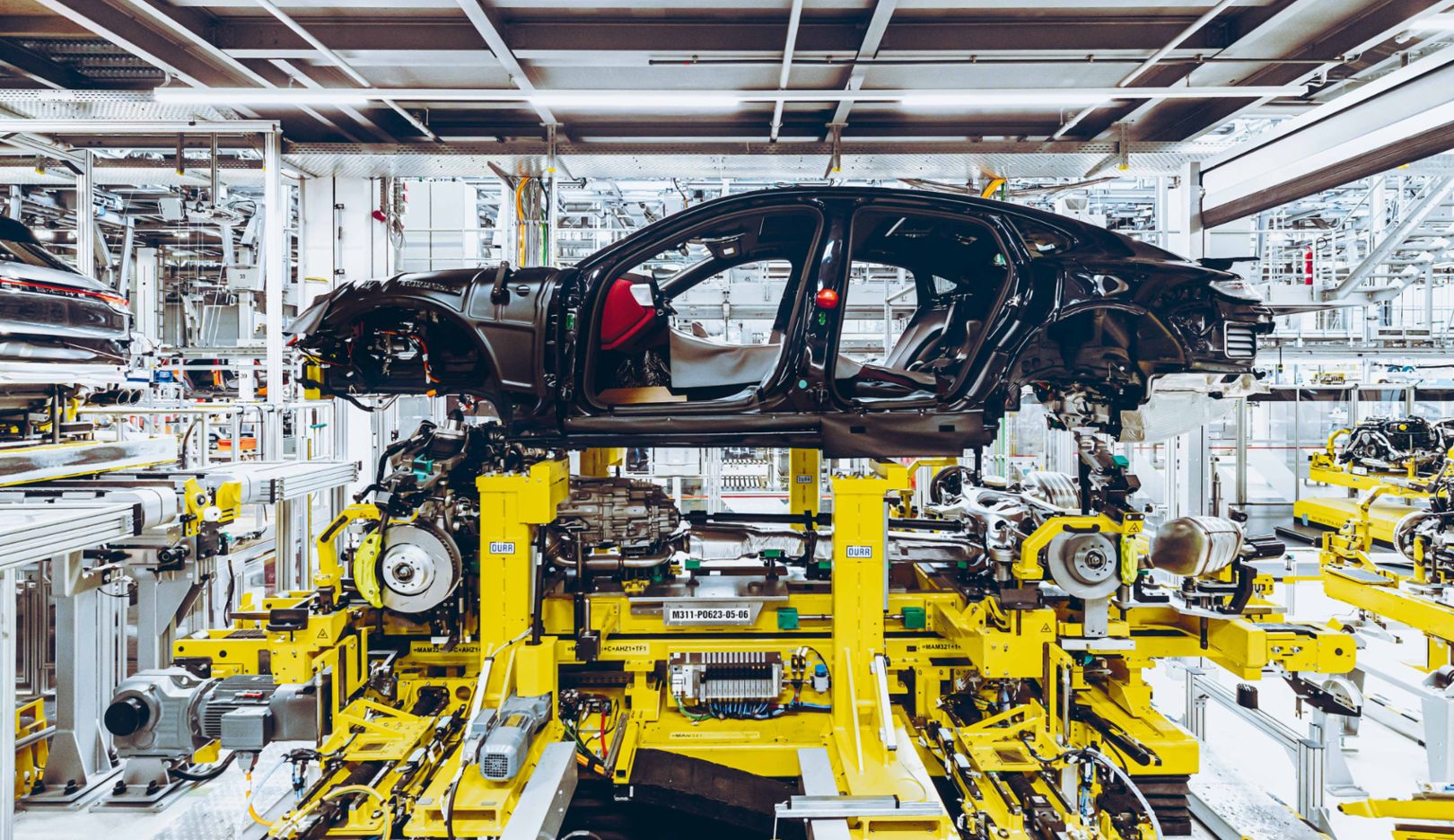
Zaawansowany technologicznie mariaż:
The body, engine, and chassis are joined in a fully automatic process.Bezpośrednio po stacjach konstrukcji karoserii, lakierowania i montażu każdy egzemplarz wjeżdża na zbudowany przy zakładzie tor kontrolny. „Poza tym”, objaśnia Rupp, „każdemu klientowi, który odbiera od nas samochód osobiście, udzielany jest na torze instruktaż. Oczywiście nie w jego pojeździe prosto spod igły, lecz w takim samym modelu”. Na taką atrakcję decyduje się nawet 2800 klientów rocznie.
Pętla o długości 3,7 km rozciąga się przed „Diamentem”. Wijącą się wstęgę zaprojektował Hermann Tilke, architekt torów wyścigowych na potrzeby Formuły 1. Sześć odcinków do jazdy na pełnej prędkości, sześć punktów hamowania. Tor o szerokości dwunastu metrów spełnia wymogi stawiane przed obiektami organizującymi zawody sportowe i posiada certyfikat Międzynarodowej Federacji Samochodowej (FIA). Jego uzupełnienie stanowi tor do jazdy dynamicznej o długości 2,2 km z nawadnianymi nawierzchniami do treningów kontroli i hamowania.
Podczas wbijania szpadla pod budowę zakładu nie było infrastruktury, tylko dużo wolnej powierzchni, która została następnie zaplanowana przez Porsche. Pod względem historycznym teren o zróżnicowanej rzeźbie o powierzchni 132 ha reprezentuje różne światy. To, co dzisiaj służy konstruktywnym celom, niegdyś miało charakter destruktywny. Od czasów Cesarstwa Niemieckiego do 1999 roku teren ten służył zmieniającym się reżimom do celów militarnych. Dzisiejszy tor do jazdy terenowej o długości 6 km obejmuje nawet dawne bunkry. Ścieżka offroadowa oferuje 15 modułów – łącznie ze stumetrową przeprawą wodną i ekstremalnym podjazdem o nachyleniu 80 procent. Ten wyjątkowy plac czyni nie tylko odbiór w zakładzie niezapomnianym przeżyciem. Centrum obsługi klienta przekształcone w Porsche Experience Center zapewnia kierowcom o zacięciu sportowym z całego świata emocjonalne doznania za kierownicą. Poza tym możliwość zwiedzenia zakładu i skorzystania z wyśmienitej oferty gastronomicznej – od niedawna także dla spontanicznych gości.
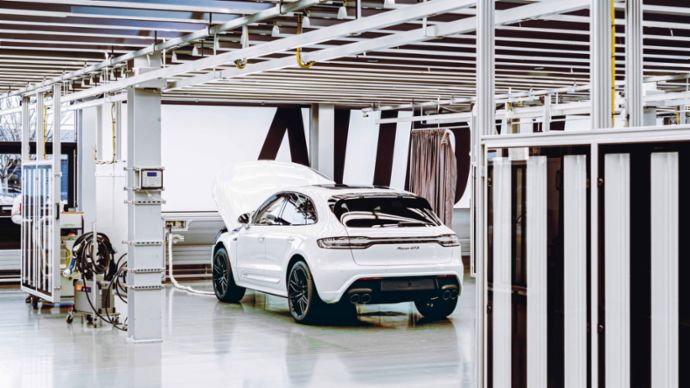
Wysokie standardy jakościowe:
Vehicles are randomly selected and put through their paces in daily audits. Special lighting reveals every detail.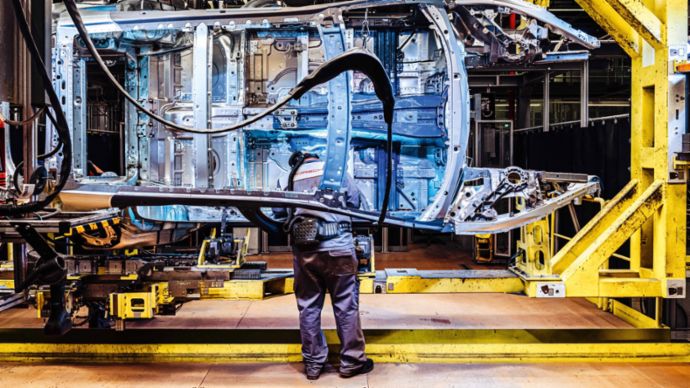
„Dla Freda nie ma to żadnego znaczenia”, mówi z uśmiechem Rupp. Szef stoi na łące przed zakładem. Naprzeciwko niego stoi byk Hecka – ta rasa jest próbą odtworzenia wymarłego już tura. Porsche ulokowało ich tu 75. Fred czuje się dobrze w skrupulatnie zrenaturyzowanym środowisku. W towarzystwie 25 wolno żyjących kuców Exmoor, trzech milionów pszczół miodnych oraz rozlicznych dzikich zwierząt. „Ponosimy odpowiedzialność ekologiczną – zarówno w halach zakładowych, jak i poza nimi”, podkreśla Rupp. Podczas gdy ptaki, sarny i borsuki cieszą się nowym domem na idyllicznych błoniach, zrównoważony rozwój jest uskuteczniany również w produkcji. Dzięki racjonalnemu wykorzystywaniu surowców, materiałów i środków produkcji oraz optymalizacji procesów.
Lista wyróżnień przyznanych zakładowi jest długa. Zdobył on między innymi liczne nagrody za działalność na rzecz ochrony środowiska, różnorodności biologicznej, ekologicznego bilansu energetycznego oraz optymalnego wykorzystania surowców. W 2021 r. przykładowo Lean & Green Management Award. Zgłoszono 250 zakładów z ponad dziesięciu krajów i reprezentujących 20 gałęzi przemysłu.
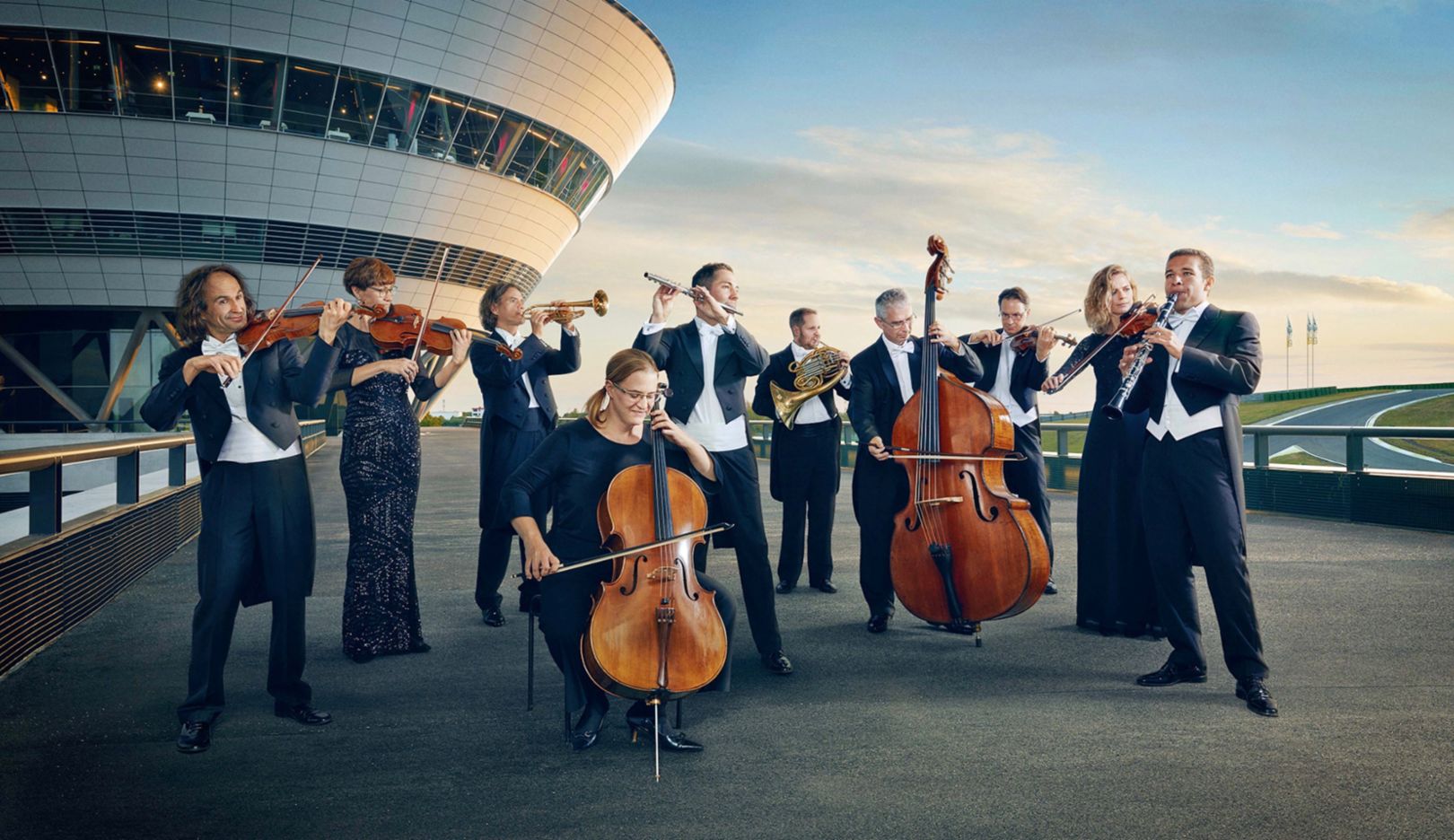
Harmonijny mecenat:
Porsche and the Leipzig Gewandhausorchester have been working together since 2011.Produkcja w Lipsku jest zasilana prądem pochodzącym w stu procentach z odnawialnych źródeł energii. Same tylko własne instalacje fotowoltaiczne dostarczają nawet 5000 megawatogodzin rocznie. Elektrownia na biomasę zlokalizowana bezpośrednio przy zakładzie pokrywa zapotrzebowanie lakierni na energię cieplną w 80 procentach neutralnie pod względem emisji CO₂. Biorąc pod uwagę bilans ogólny, cały zakład jest obecnie neutralny pod względem emisji CO₂. Niedługo będzie mieć status Zero Impact Factory. Czyli lokalizacji produkcyjnej, która nie pozostawia śladu ekologicznego.
„Szczególnie dumny jestem z naszego ośrodka szkoleniowego”, mówi Rupp, zmieniając temat. „Wspaniale jest obserwować, jak młodzi ludzie rozpoczynają tu karierę”. Dobudowany obiekt otwarty w roku szkoleniowym 2021/2022 ma powierzchnię 1600 metrów kwadratowych. Kształcenie zawodowe w zakładzie rozwijało się przez dwie dekady: od pięciu praktykantów w chwili otwarcia po 120 początkujących adeptów zawodu. Przychodzą, by pozostać. Wpisuje się to także w filozofię uczenia się przez całe życie jako klucza do sukcesu. Wykwalifikowany personel regularnie dokształca się w centrum szkoleniowym.
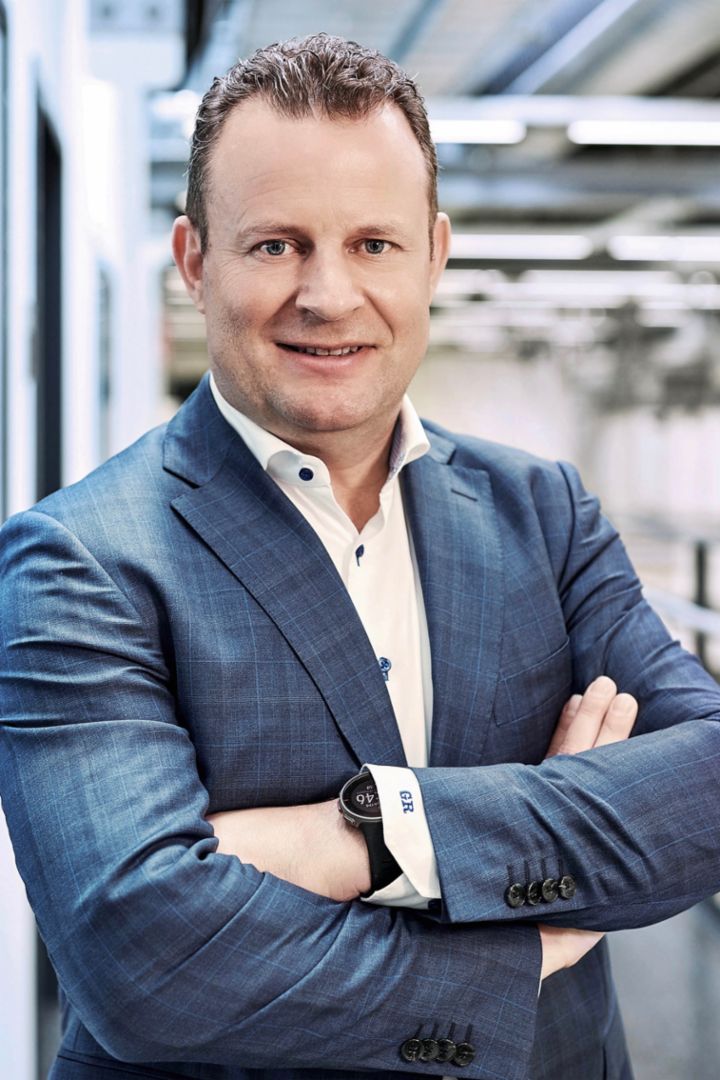
Pracownicy Porsche cieszą się w Lipsku poważaniem. Przedsiębiorstwo zapewnia miejsca pracy, a atrakcyjnymi ofertami zwabia turystów z całego świata do targowego miasta. Producent wozów sportowych jest mecenasem słynnej lipskiej orkiestry Gewandhaus, finansując koncerty dobroczynne i organizując wydarzenia kulturalne dla społeczeństwa. W tym roku ofertę kulturalną zakładu uzupełni Wagner 22 – festiwal operowy na cześć urodzonego w Lipsku kompozytora Ryszarda Wagnera. Pod względem sportowym Porsche realizuje wieloletni program Turbo für Talente we współpracy z klubem RB Lipsk z pierwszej Bundesligi. „W zakresie edukacji programami szkoleniowymi w zakładzie oraz stypendiami akademickimi wspieramy przede wszystkim dzieci, młodzież i studentów o słabszej pozycji społecznej”, wylicza dalej Gerd Rupp. Od 2013 r. przedsiębiorstwo utrzymuje także ufundowaną przez siebie katedrę zarządzania w Wyższej Szkole Handlowej w Lipsku. „Pojawiliśmy się tu”, podsumowuje dyrektor zakładu, „otrzymujemy wiele, ale także wiele oddajemy temu miejscu”.
„Nasz sukces zawdzięczamy w dużej mierze naszej załodze”.
Gerd Rupp
550 pojazdów
Tyle egzemplarzy modeli Macan i Panamera wytwarza się każdego dnia w lipskim zakładzie.
88 procent
Zdecydowana większość pojazdów ma kierownicę z lewej strony. Wysyłka na cały świat odbywa się bezpośrednio z zakładu bocznicą kolejową.
3 zmiany
Od poniedziałku do piątku prace toczą się non stop w trybie zmianowym. W weekendy taśmy zazwyczaj stoją w miejscu.
18 procent
Najczęściej wybierane wyposażenie niestandardowe obejmuje fotele sportowe. Są one montowane w niemal jednej piątej wszystkich pojazdów.
1000 robotów
W lipskim zakładzie Porsche wykorzystuje się ultranowoczesne specjalistyczne roboty. Ułatwiają one realizację prac.
430 elementów
Metodami spajania mechanicznego i termicznego łączy się komponenty w karoserii Panamery.
Zużycia paliwa/prądu
Macan GTS
-
11.7 – 11.3 l/100 km
-
265 – 255 g/km
-
G Class
-
G Class