The obstacle is directly behind a curve: A large branch blocking the road. A vehicle turns into the corner—and immediately unleashes a digital cascade. The front camera detects the obstacle and the evaluation algorithm connected to it sounds the alarm. It classifies the branch as a hazard and initiates braking. At the same time, it reports the position and the type of obstacle to a cloud server using the mobile network. Other drivers who are also approaching the hazard area now see the ‘Obstacle’ warning message on their dashboard, including the distance to the branch on the roadway. This enables them to prepare for the hazard well in advance.
This scenario is supposed to soon be a reality, as vehicle-to-X (V2X) communication is making rapid advances. In just a few years’ time, vehicles should remain in constant contact with each other and their environment. They will then be able to exchange information with pedestrians’ smartphones or with a set of traffic lights. V2X is supposed to help prevent accidents, improve the flow of traffic and make advanced driver assistance systems (ADAS) more effective.
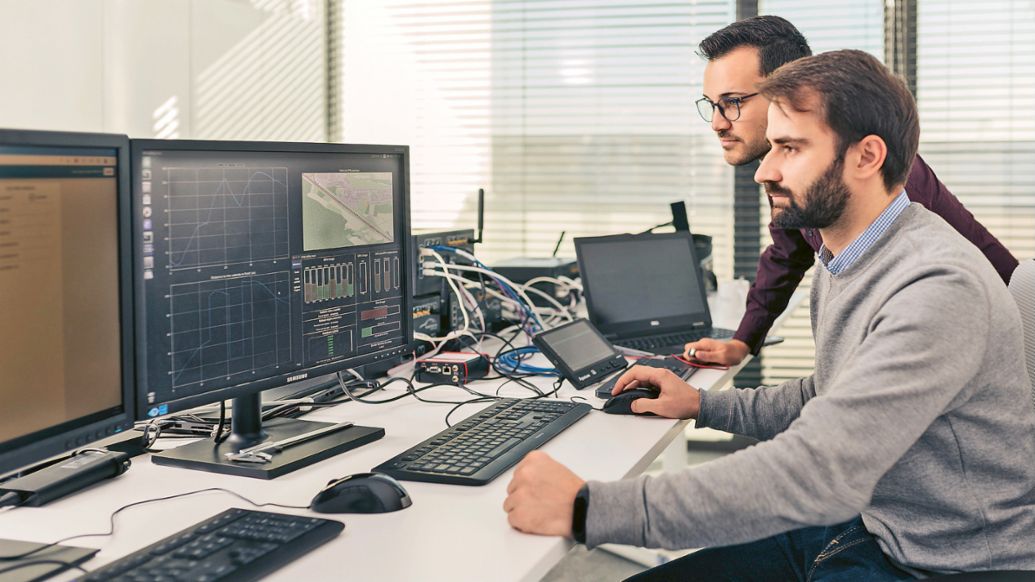
“The vehicle of tomorrow will not only use its own sensor technology, but also other road users’ sensor systems,” explains Pasqual Boehmsdorff, Project Leader for V2X Function at Porsche Engineering. “This makes V2X an important step forward on the road to fully autonomous driving.” China is currently a pioneer when it comes to V2X. In the metropolis Wuxi, many sets of traffic lights are connected to a traffic control center that tells drivers when the next run of green lights is coming. What’s more, the networking of road users is being trialed in the metropolitan area: If the vehicle’s on-board sensors register, for example, that the road surface is slippery, it can send this information to a central server that relays it on to other vehicles. Porsche Engineering is also already conducting intensive real-world tests with V2X technology at its development center in Anting near Shanghai.
A large number of new functions
The new technology that is also being used in these parts could make a large number of helpful functions possible: A live traffic light information function, for one, could be connected to the distance cruise control and thereby modify the speed so that the driver only has to wait at the traffic lights for the shortest time possible, and would thereby be able to drive more efficiently. A digital extension of the warning triangle would also be possible: If the vehicle stopped with its hazard warning lights on, nearby road users would be informed by direct short-range communication. This hazard warning could also be forwarded to a central server so that road users who are not in the immediate vicinity could also access it.
In principle, there are two technical concepts that are used for connecting vehicles. One is the 802.11p standard, a variant of Wi-Fi. It allows vehicles to communicate with each other directly. If they are more than 200 to 300 meters apart, roadside units (RSUs) are needed along the road to relay the signals. Installing these routers is costly, but this said, Wi-Fi is considered a fully developed technology. The second option is to use the existing cellular network. The corresponding standard is called C-V2X (the ‘C’ stands for ‘cellular’).
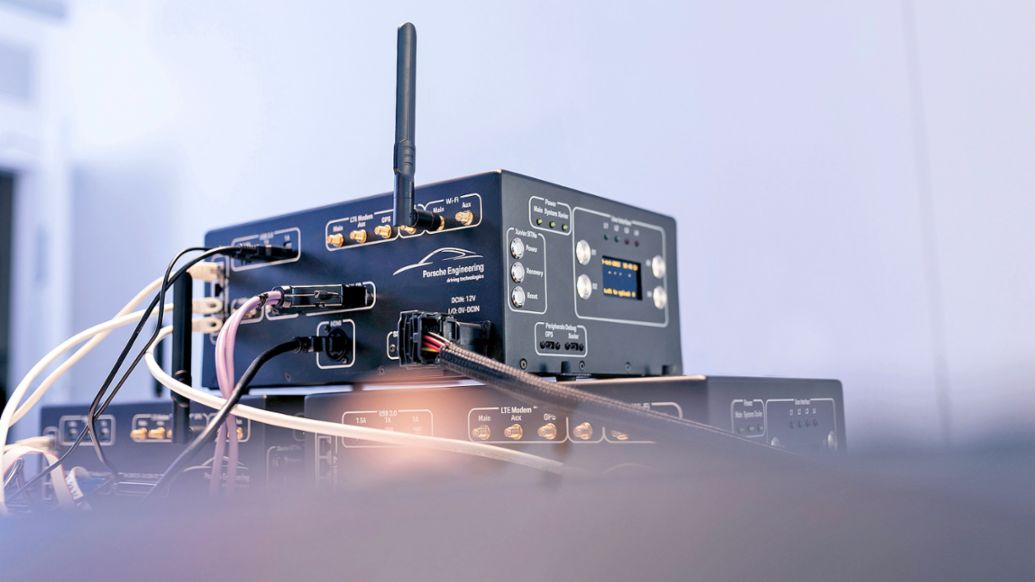
It was initially based on the 4G/LTE cellular standard, and all data had to be sent using a base station. The latest, 5G-based version also makes direct communication between vehicles possible (using what is called a sidelink/PC5 interface). Europe and the US had initially opted for 802.11p, however two years ago the US regulator FCC withdrew the radio frequencies necessary from the standard. For its part, China is pushing ahead with 5G-based networking: By 2025, every second new car in the People’s Republic is expected to be permanently online.
“The vehicle of tomorrow will not only use its own sensor technology, but also that of other road users’ sensor systems.” Pasqual Boehmsdorff, Project Leader V2X Functions at Porsche Engineering
“This is why I am assuming that a system based on mobile communications will prevail for V2X,” says Thomas Pretsch, Senior Manager Connectivity at Porsche Engineering. The implementation of a new V2X function starts with software development. In the case of the obstacle warning that was described at the beginning of this article, this involves the use of artificial intelligence (AI): A neural network is trained using recordings of real driving situations to allow it to recognize and classify obstacles—and this continues until it can distinguish real hazards (for example, pedestrians, or branches) from harmless objects (leaves, plastic bags) with one hundred percent certainty. Since there is often little real-life training material for dangerous situations in particular, it is supplemented with synthetic data.
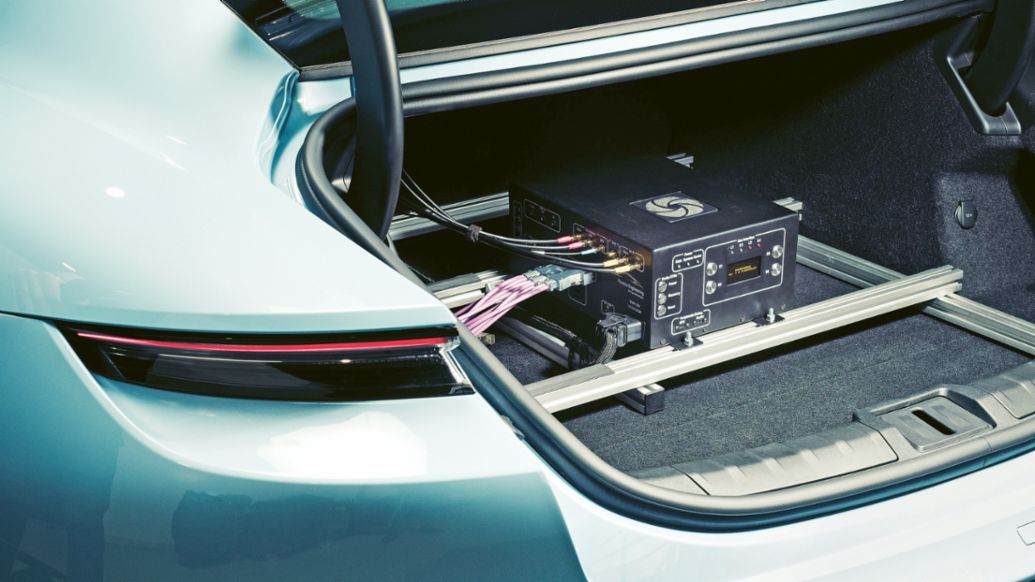
“We vary the actual driving situation virtually,” explains Dr. Joachim Schaper, Senior Manager AI and Big Data at Porsche Engineering. The tool used for this is called PEVATeC (Porsche Engineering Virtual ADAS Testing Center). It replicates a physical environment exactly—not only the visible surroundings with roads and vehicles, but also the sensor data that would be available in the vehicle bus in the corresponding situation. This makes it possible to run through the ‘branch on the roadway’ hazard situation in countless variations: With the glare of the sun in the background, when it is dark, or when heavy rain is falling. After all, AI has to classify the object correctly in all conditions.
Tiered countermeasures
After training, the engineers copy the neural network to the component called the Car Data Box (CDB, see box). This development computer, which was developed at the Porsche Engineering location in Cluj-Napoca and Timișoara, Romania, is installed in the test vehicle and can run any ADAS program. The CDB uses the neural network to evaluate real camera and sensor data for the obstacle warning. A special algorithm determines whether an object exceeds a hazard threshold and initiates countermeasures according to a tiered system: From a mere message on the dashboard to an acoustic warning signal or, ultimately, autonomous braking.
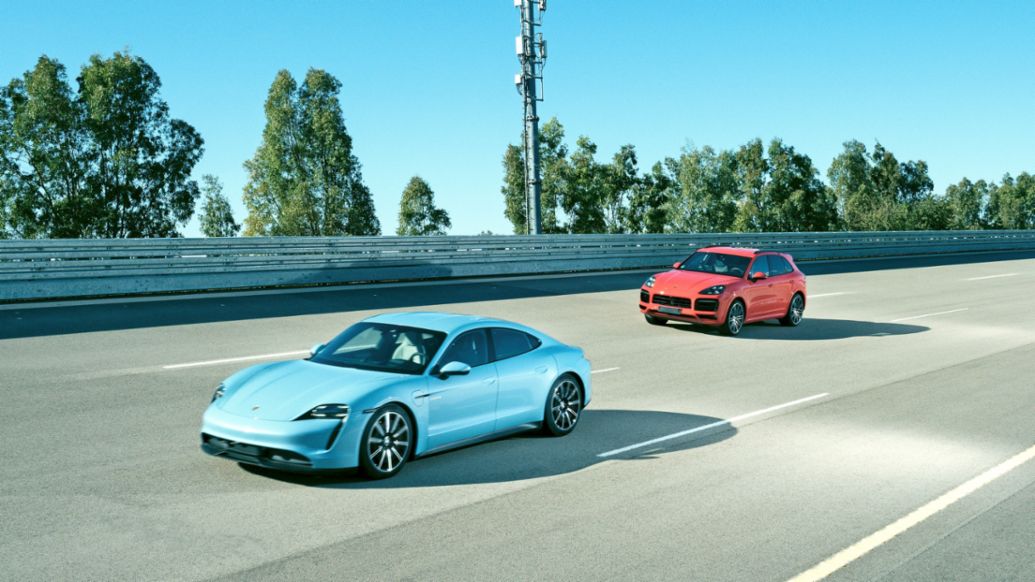
In the final step, the function is tested in real conditions. The Nardò Technical Center (NTC) offers ideal conditions for this, as the entire 700-hectare site is equipped with a private 5G network. This is where engineers can check whether a warning message, once issued, reliably reaches its recipients in real-life conditions as well. “The correlation between vehicle speed and data throughput is crucial in this case,” explains Luigi Mazzarella, a telecommunications expert at the NTC.
Engineers tested how fast data travels at high driving speeds in the summer of 2022. Several vehicles completed laps of the 12.6-kilometer high-speed circuit while their Car Data Boxes were sending data. The result: At speeds of up to 100 km/h, data rates remain almost constant—1 gigabit per second for downloads and around 150 megabits per second for uploads. At speeds above 200 km/h, the upload speed decreases slightly to 120 megabits per second, while there is no change to reception rates. The bandwidth only decreases at significantly higher speeds, but still remains sufficient at 90 megabits per second for data upload.
The tests showed that both the bandwidth and the latency in the 5G network are sufficient for automotive applications. Handover, this being the transition from one base station to the next, was also intensively tested. In earlier wireless generations the connection could break off, however 5G ensures the handover succeeds reliably even at high speeds. For the development of V2X functions, the specialists at Porsche Engineering no longer have to travel to the test track in Apulia. The current version of the Car Data Box is equipped with a 5G module, which makes it possible to install test programs remotely.
“We vary the actual driving situation virtually.” Dr. Joachim Schaper, Senior Manager AI and Big Data at Porsche Engineering
After or during the test drive, the Car Data Box uses 5G to send all data back to the cloud, where it can be analyzed and enriched. “Driving on the one hand, and evaluation and implementation on the other, are therefore independent of time and location,” says Schaper approvingly. Remote access will allow new functions—including those for connected driving—to literally make it to the road faster in the future.
The Car Data Box
The Car Data Box (CDB) is a development computer connected to the data bus and sensor technology of a test vehicle. It is ideally suited for implementing new driver assistance systems for which standard ECUs are not powerful enough. The core of the CDB is a Graphics Processing Unit (GPU) from the manufacturer NVIDIA, which is particularly good at machine learning applications.
The test computer is a project being pursued by the Porsche Engineering locations in Cluj-Napoca and Timișoara (Romania), which also developed the requisite software. Engineers at the Prague location were responsible for the hardware side of things. The first version of the CDB was unveiled in June 2020, and it has been in continuous development ever since. A 5G module, for example, has been improving the cloud connection since 2021. Integration of the Robotic Operating System (ROS) also facilitates development work: ROS converts the data from cameras, radar or lidar sensors into a format that does not depend on the specific technology. For example, if a new camera with a higher resolution is installed in the test vehicle, the existing evaluation algorithms can continue to be used. This obviates the need for new development.
Summary
In just a few years’ time, vehicles are supposed to remain in constant contact with each other and their environment (V2X). To develop V2X functions, Porsche Engineering uses virtual development methods that make it possible to play out situations in countless variants. An important development tool here is the Car Data Box, which can execute any V2X function. Tests are also carried out on the 5G network at the NTC, which was set up specifically for this purpose.
Info
Text first published in the Porsche Engineering Magazine, issue 1/2023
Text: Constantin Gillies
Photos: Luca Santini; Chris Nemes
Copyright: All images, videos and audio files published in this article are subject to copyright. Reproduction in whole or in part is not permitted without the written consent of Dr. Ing. h.c. F. Porsche AG. Please contact newsroom@porsche.com for further information.