Mission E
Breaking new ground and promptly taking the lead. Doing everything differently yet still decisively stamping classic Porsche virtues on the electric era. The world expects no more and no less of the first purely electric Porsche when it makes its debut in 2019. A dossier on the subject of electromobility.
Mission E becomes Taycan
The future of mobility is another step closer: Series production of the first purely electric Porsche is set to begin next year. In preparation, the vehicle has now been given its official name: The “Mission E” concept study, the name currently used to describe Porsche’s complete electric offering, will be known as the Taycan.
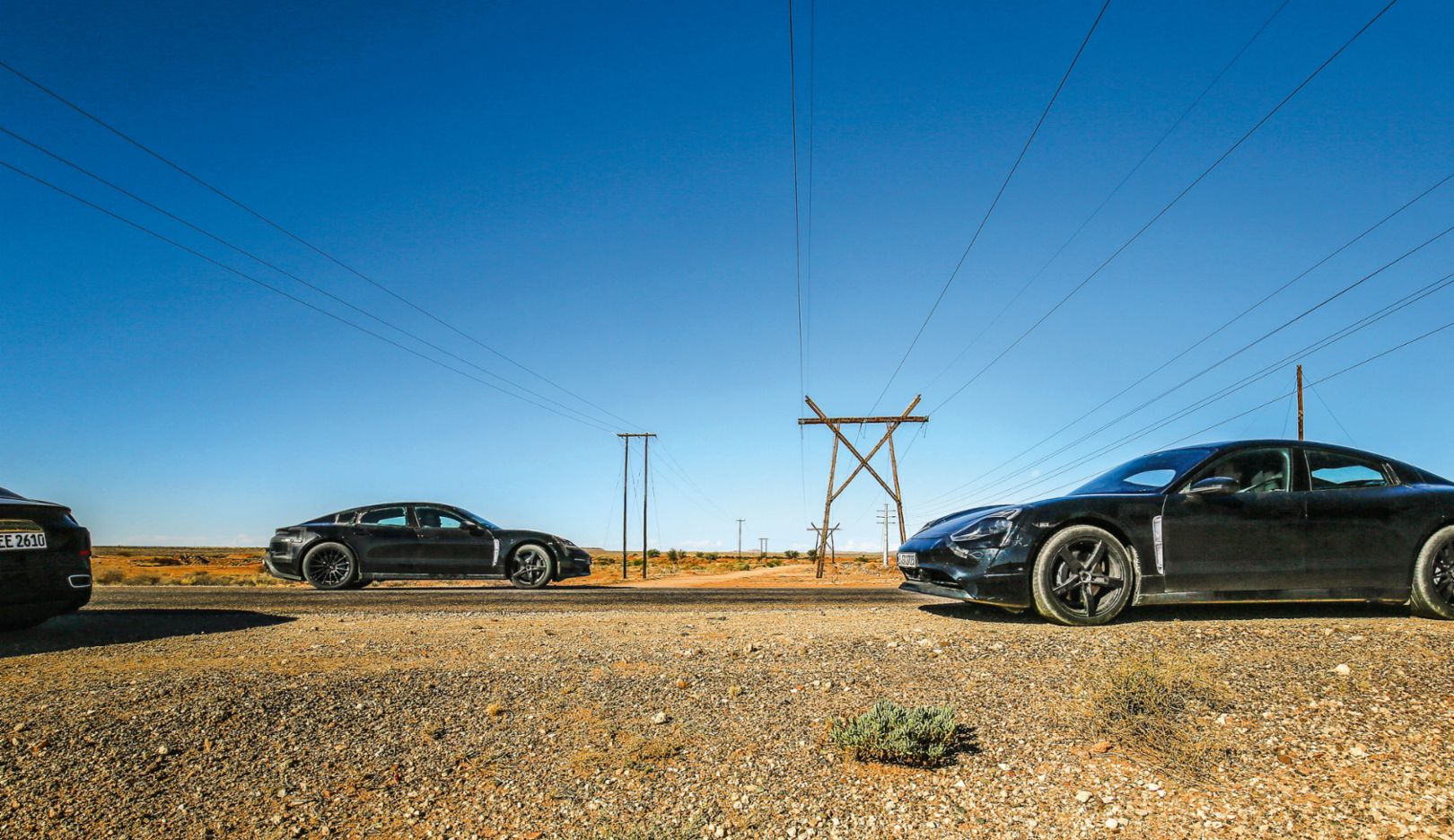
Out in the open
The Taycan is still a confidential undertaking. Yet the purely electrically powered sports car from Porsche is already out and about on public roads—on intensive testing tours in extremely hot and bitterly cold regions of the world. One station: the western part of South Africa. More than sixty Porsche developers were on hand with twenty-one camouflaged prototypes—with daily high temperatures of around 40 degrees Celsius proving a challenge for the team and the machine in equal measure. All in all, some forty thousand kilometers were banked on the trip. By the time the Taycan hits the market in late 2019, the total will run into the millions of kilometers. The first electric sports car from Porsche, after all, should run like clockwork in even the toughest conditions.
> 600 hp (440 kW)
The Taycan stands for total system performance.
800 V
The components of the Taycan drive system work with this voltage. New terrain, even for the prototype builders.
Ca. 40 specialists
build the prototypes of the Taycan at Porsche.
3 figures
worth of prototypes of the Taycan have been built to date. The exact number? Confidential!
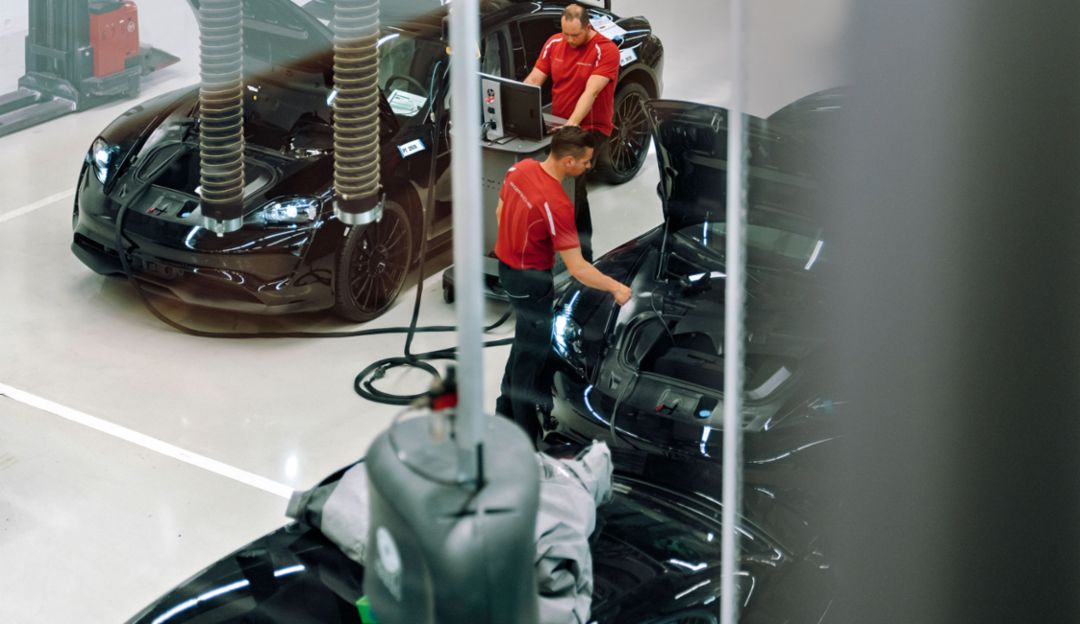
Behind closed doors
Those who work there know the Porsche Taycan inside and out before the rest of the world ever lays eyes on it: the prototype construction department in Zuffenhausen is the birthplace of every new Porsche model. The 800-volt technology of the first purely electrically powered Porsche, its battery system, the complex cooling system: what the designers imagine for the Taycan is translated into initial test cars by the specialists in the closely guarded prototype construction department. At the same time, they lay the groundwork for series production, because they test and perfect all the necessary assembly and logistics concepts. They also train their colleagues from the assembly teams to ensure an optimal preparation for the Taycan’s series production.Drive unit
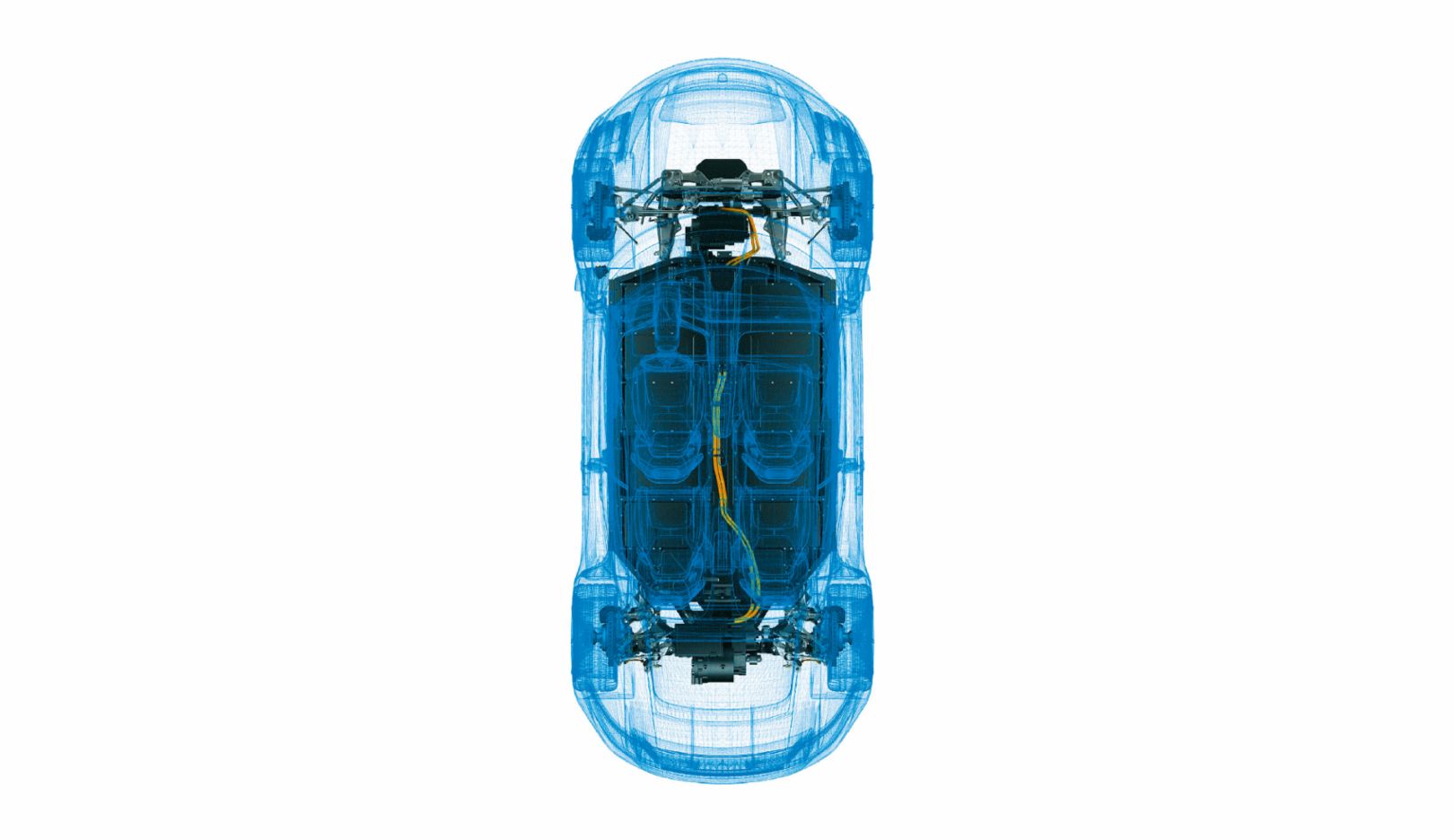
> 500 km
With a range of over 500 kilometers, the Taycan isn’t just sporty—it’s also practical.
> 600 hp
are packed and ready for action by two permanently excited synchronous motors (PSM).
800 V
is the voltage with which the components of the Taycan’s drive system works.
< 3.5 sec.
is all the Taycan needs to go from 0 to 100 kmh. The enormous torque from the very first rev delivers sporty acceleration.
→ THE SITUATION
Greater environmental protection, new markets, less dependence on fossil fuels: mobility and automobile manufacturing in particular are being reimagined. The ongoing development of electromobility is a future-shaping topic in the industry worldwide. It’s the key to environmentally friendly mobility. Policy is an important factor here. By 2020 European auto manufacturers have to bring their new cars up to a fleet average of just ninety-five grams of carbon dioxide emissions per kilometer.
For Porsche the future is electric. By 2025 the aim is for every second Porsche sold to have an electric drive unit.
And the number of electric vehicles worldwide is indeed on the march. The total number of electrically powered cars reached some 3.2 million in early 2018. That’s a 55 percent increase over the previous year. The figure includes all vehicles charged with electricity, such as plug-in hybrids. The market is driven primarily by China. There are currently over 1.2 million electric cars there, with 579,000 of them added in 2017 alone. In the US, the number of electric vehicles rose by 195,000 in 2017 to a total of over 750,000. Germany has comparatively low figures, but they did rise by 54,490 to 92,740 vehicles in total. The share of new registrations came in at 1.6 percent. If the growth rate stays near the level of 2017, the number of annual new registrations for electric vehicles worldwide will exceed twenty-five million by 2025.
For Porsche the future is electric. The company wants to shift to electromobility before all other German auto manufacturers. By 2025 the aim is for every second Porsche sold to have an electric drive unit. Porsche will release its first electric model, the Taycan sports car, in 2019. Current estimates project roughly twenty thousand units a year. That would be equivalent to roughly two-thirds of the current sales figures for the 911.
→ THE CHALLENGES
Electrification in the carmaking field is driven in equal measure by regulations in the areas of nitrogen oxides and CO₂ and urbanization. The world is gathering in cities—everywhere. Since 2007 as many people have lived in cities as in rural areas. In parts of Asia and Africa, urbanization is reaching a breakneck pace. Megacities like Tokyo, Mumbai, and Shanghai provide a glimpse of the course of advancing urbanization.
The effects on the automotive industry are immense. The most important task for Porsche is to play a role in shaping these changes—with vehicles that are sporty, unique in terms of design, and marked by high day-to-day usability thanks to a high range. The challenges: How do you create an electric vehicle that sets new standards in terms of performance and efficiency, driving dynamics, and day-to-day usability? How do you compensate for the weight of the batteries? What can enable an electric vehicle to feel like a typical Porsche?
→ THE PORSCHE WAY
For the first purely electric Porsche, the engineers in Weissach developed a drive concept based on the principle of intelligent performance—a principle woven into the fiber of every Porsche. “We opted for a permanently excited synchronous motor in the Taycan,” reports Heiko Mayer, drive unit project leader. “They combine a high energy density with strong sustained performance and maximum efficiency.” Two permanently excited synchronous motors (PSM), like those deployed in the Le Mans–winning 919 Hybrid, generate a permanent rotary motion that can be applied at any time without needing to be started—a technical feat achieved by having a permanently magnetized rotor forced into a rotary motion by the magnetic field of the stator.
PSM electric motors are the turbos of the electric motor milieu. They boast both extremely high sustained performance and maximum efficiency. One motor powers the Taycan’s rear axle, the other the front wheels. Together they generate over 600 hp (440 kW) and are fed by batteries designed to provide five hundred kilometers of range. The Taycan sprints from 0 to 100 kmh in well under 3.5 seconds and tops 200 kmh in under 12. The PSM drives convert electrical energy into power with great efficiency, smoothness, and sustained output while generating relatively little heat. A Porsche with electric drive technology is naturally track-ready as well.
The PSM motors also enable a very compact design. As Mayer observes, “That makes it possible to make the motors and batteries smaller and lighter with the same power figures.” And to save even more space, the electric motors’ solenoid coils feature a so-called hairpin technology design. “The coils are made of wires that aren’t round, but rather rectangular,” explains Naser Abu Daqqa, director of electric drive systems at Porsche. “This makes it possible to pack the wires more tightly and get more copper into the coil machines—increasing power and torque with the same volume.” The Taycan’s power electronics are also fine-tuned for efficiency. The inverters that convert the battery’s direct current into alternating current for the electric motor don’t work with a fixed pulse frequency as is common, but with a steplessly variable pulse frequency. “So the motor always runs at the optimal operating point,” explains Mayer. Intelligent performance is also delivered by the cooling system. Temperature sensors detect the cooling requirements in real time, while software ensures that the cooling water is immediately directed to the right spots. If the driver floors it, the cooling kicks into high gear as well, ensuring constant power.
Battery
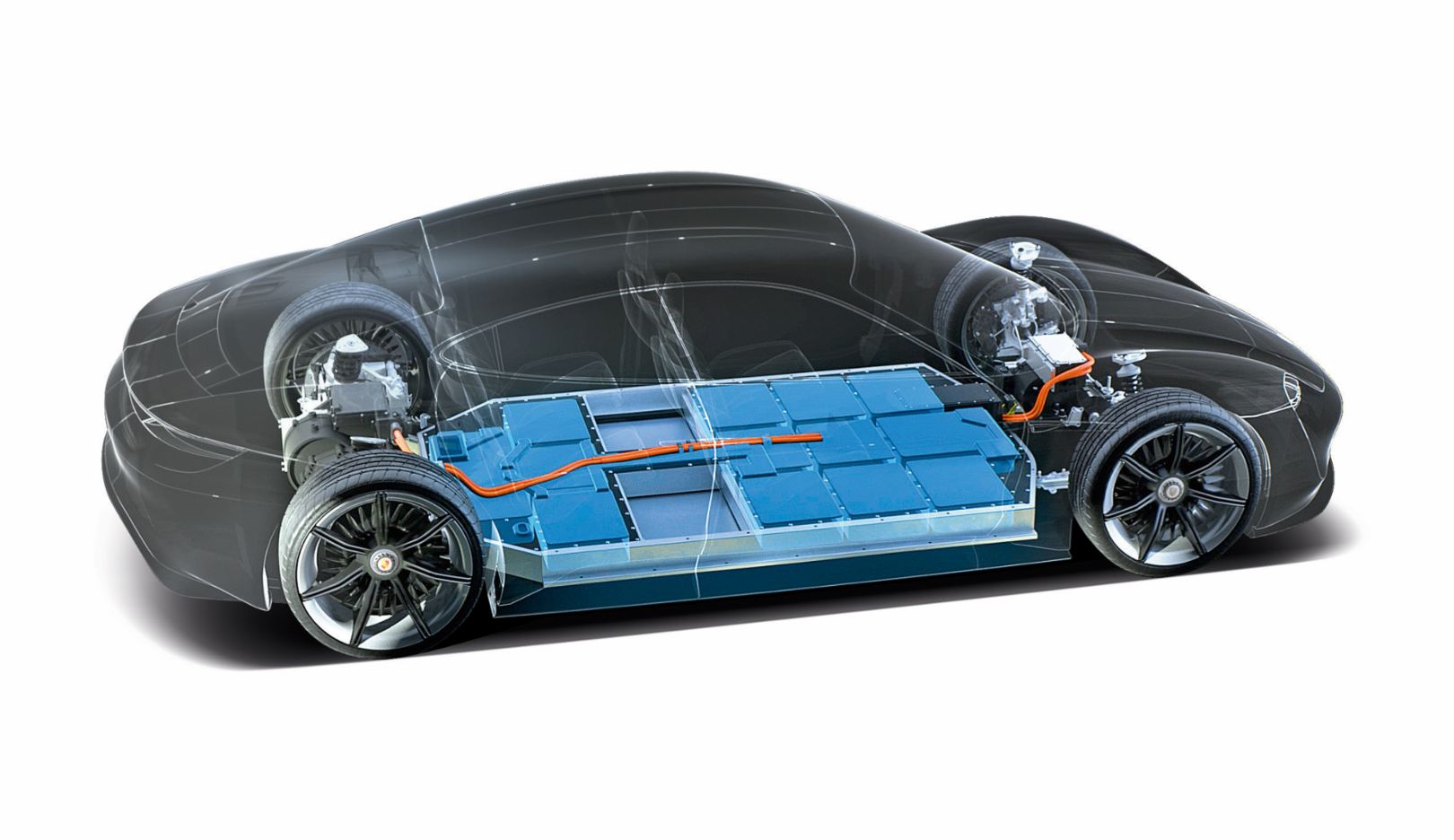
Range
is one of the most important criteria for the buyers of electric vehicles.
20 to 40°C
is the optimal operating temperature for a lithium-ion battery.
€ 6 bn
will be invested in electromobility by Porsche through 2022.
4 V
are packed into each of the cells in an 800-volt battery.
100 %
green energy is used by Porsche at its German production facilities.
→ THE SITUATION
Batteries are the heart of electrically powered vehicles. Compared to combustion engines, however, electric vehicles are regarded as more expensive and enjoy only limited acceptance today due to their lower ranges and the still-inadequate coverage and supply infrastructure. And the safety of the batteries is a source of concern for some vehicle buyers as well. The technology of the batteries is complex and presents new challenges for the manufacturers. The requirements of the batteries for use in electric models are extremely demanding.
“Range is one of the most important criteria for buyers of electric vehicles,” says Otmar Bitsche, director of E-Mobility at Porsche. High-voltage batteries using the latest lithium-ion technology are currently the gold standard. Their specific energy content is currently roughly 270 watt-hours per kilogram (Wh/kg). But like the development for cell phones and their batteries, development of the battery technology proceeds at a continuous rate of up to 5 percent annually.
The growing importance of electromobility pushes developers worldwide to come up with the best possible solutions, with research focusing on both optimizing the existing lithium-ion technology by extending into new materials and completely new battery technologies based on solid-state electrolytes.
→ THE CHALLENGES
Three essential factors define the development. One: the weight. Two: the temperature. Three: the availability of raw materials. Theoretically, ranges of over five hundered kilometers are already possible today, albeit with a serious handicap: the weight of the technology. Lithium ions are therefore packed together as tightly as possible. The more of them that fit into a battery, the more electrons and thus more energy can be stored in the same space. Doing that means changing physical and chemical processes on the atomic and molecular levels in the cell. Then there’s the fact that a battery only works perfectly at optimal temperatures. A lithium-ion battery, for example, works best between 20 and 40 degrees Celsius. That applies to both charging and driving. Finally, automobile manufacturers are also faced with two other fundamental challenges: the sufficient availability of raw materials and extracting them sustainably. Porsche is actively preparing itself for both.
→ THE PORSCHE WAY
Speed instead of weight—the Weissach motto. Rather than installing heavy batteries, Porsche opts for fast charging. Electricity flows through some four hundred cells, which are connected both serially and in parallel. Each individual cell has a current of roughly 4 volts. Controlled by the battery management system, this all amounts to the 800-volt battery, in simplified terms. “It was a major challenge to achieve such enormous battery capacity both for charging and discharging over the entire temperature range,” says Nora Lobenstein, head of all energy storage systems at Porsche. The solutions are an intelligent charging protocol and an efficient heat exchanger system that quickly gets the batteries up to operating temperature and reliably cools them under heavy loads—for example, during a sudden spike in power usage or during rapid charging. The objective of the Porsche fast-charging system: four hundred kilometers of range in about fifteen minutes. Aside from the short travel breaks for charging, another payoff of the 800-volt technology is the thinner cables in the car. That saves weight.
A Porsche has an extremely long life cycle, longer than the vehicles of other brands. Porsche batteries should have the same.
But for Lobenstein, the topic of batteries doesn’t end there. Sustainability is more than just a marketing term in Weissach. Porsche developers are already intensively studying how the Taycan’s batteries can be reused in the future. After all, a Porsche has an extremely long life cycle, longer than the vehicles of other brands. The batteries should have the same. A second life, at any rate.
Charging
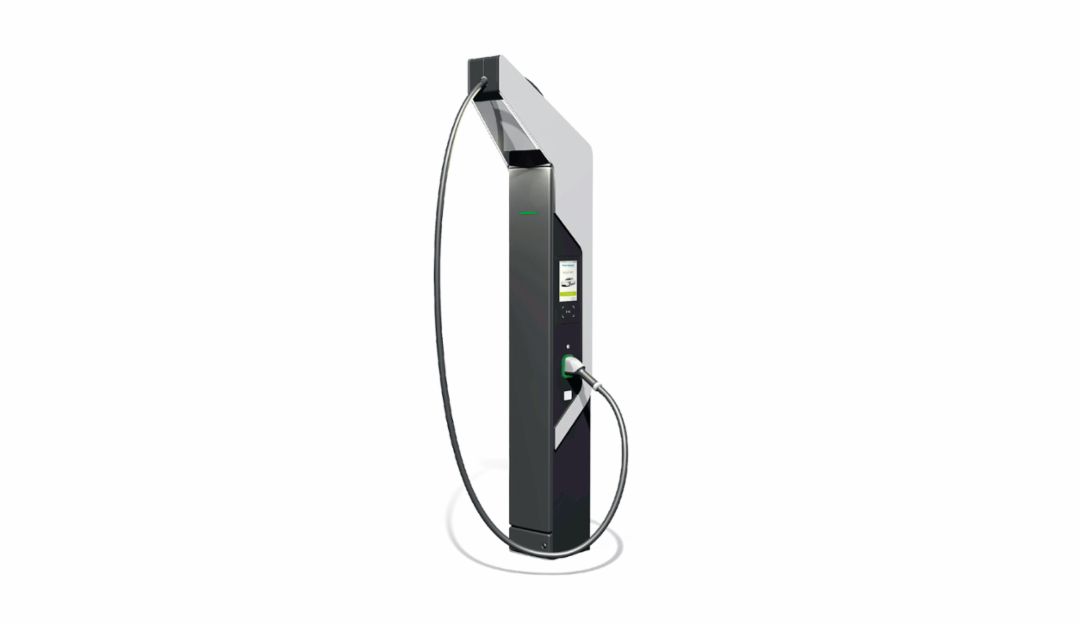
800 V
The new generation of charging stations is designed for 800-volt technology. But it’s also downward-compatible for all vehicles on the market with 400-volt technology.
15 minutes
The Taycan is ready for the next four hundred kilometers in roughly fifteen minutes.
10 inches
The large touch display is designed to allow optimal readability even in bright sunlight.
CCS
Porsche employs the Combined Charging System as the standard in Europe and the US for alternating current (AC) charging and direct current (DC) charging. For Japan and China, Porsche will offer the local standards.
→ THE SITUATION
Great distances between charging stations, no standard payment model, competing connection systems, inadequate power grids—the simple matter of getting new energy into empty batteries is anything but. International standards for adequate geographical coverage with modern charging stations for millions of electric vehicles? Still in the works. There’s a fundamental distinction between conductive and inductive charging. With conductive charging, energy is transmitted between the vehicle and the power grid through charging cables and a plug system. With inductive charging, the energy is transmitted between the vehicle and the power grid without cables through electromagnetic induction.
With conductive charging, or charging with a cable, a distinction is made between alternating current (AC) charging with a conventional 400-volt plug connection, with charging capacities of up to 22 kW, and direct current (DC) charging, with charging capacities of up to 350 kW. AC charging is normally used at home or at the workplace, while DC charging is used for fast charging on the go. For AC charging, a permanently installed wallbox or a suitable charging cable is required as the connection between the power socket and the vehicle. At public AC charging stations, a special cable with a CCS connector suffices.
The additional energy needs through 2025 will likely remain modest. Estimated increases in energy demand due to electromobility will be moderate in the different regions, with substantial jumps in demand only expected in the period through 2035. The primary reason: development in China.
→ THE CHALLENGES
Step out of the car, open the tank cap, fill up, pay—and get back on the road in a few minutes. That’s been the drill for drivers until now. The technology required for charging electric vehicles is in fact already in place, with the expansion of a charging infrastructure already in the works across Europe. But enabling an uncomplicated and fast-charging procedure for electric vehicles on motorways and urban areas requires international coordination and agreements—no easy task, to be sure. Policy answers are needed. The spottily available rapid-charging stations that currently exist seldom offer more than fifty kilowatts. It takes roughly an hour of charging time to deposit enough electrons in the battery to power the next stretch of 250 kilometers. The operative questions, therefore: How can we charge faster? How can we get enough universal charging points? And how can we strengthen weak power grids?
→ THE PORSCHE WAY
It’ll take years to build a comprehensive charging network for electric vehicles. To speed up the process, Porsche is rolling up its sleeves. “Faster charging will only work with a higher charging capacity; that was clear from the outset,” says Fabian Grill, who’s working on the expansion of the charging infrastructure for Porsche. His colleagues had already established one important prerequisite: the Taycan, the first purely battery-powered Porsche sports car, works with an 800-volt battery. In order to be able to make use of these technical possibilities in the public sphere, Porsche is pushing the expansion of a fast-charging infrastructure.
The company is pursuing three options: First, charging at home—possible with a charging station or inductively via a base plate in the floor. Second, charging in cities—possible through existing infrastructure. And third, charging along the main traffic arteries in Europe. The joint venture Ionity was formed to do just that. Together with the BMW Group, Daimler AG, the Ford Motor Company, and the Volkswagen Group with Audi, Porsche is laying the groundwork for the establishment of a powerful fast-charging network for electric vehicles in Europe. The construction and operation of some four hundred fast-charging parks by 2020 are important steps toward making electromobility viable for long-distance routes as well and thus establishing itself on the market. Every Ionity fast-charging park will have multiple charging points. They ensure that a vehicle can be charged every 100 to 150 kilometers along the European road network. As the number of electric vehicles grows, so too will the infrastructure. Thus by 2020, customers will gain access to thousands of brand- and capacity-independent “high-power charging” (HPC) points. The charging capacity of up to 350 kilowatts per charging point enables accordingly designed vehicles to achieve significantly shorter charging times compared to the systems available today.
Porsche and its development subsidiary Porsche Engineering are pursuing an in-house modular concept for ultra-fast charging parks.
“Plug in and charge fast” is the motto. Payment is completely automatic. Porsche and its development subsidiary Porsche Engineering are pursuing a modular in-house concept for ultra-fast charging parks. Whether it’s individual stations in the countryside or dozens of charging stations along highways: the solution is an intelligent system with practically unlimited scalability. And that’s important to making charging parks efficient and profitable. For Porsche customers, the main priority is being able to charge their vehicle rapidly even where the local power grid is weak. That’s now possible thanks to intermediary buffer batteries, which always have enough capacity on hand. Specifically, this means fast charging in about fifteen minutes for a range of four hundred kilometers at every Porsche charging point. Operation of the charging stations via touch display is roughly as intuitive as an ATM and just as secure. The expansion of the charging infrastructure is moving forward in the USA and China as well.
The solution from Porsche can, incidentally, be used universally for any electric vehicle. The control electronics detect what type it is and reduces the charging current if the model isn’t designed for fast charging. With this infrastructure, a pioneering spirit is translated into reliable practicality and range security.
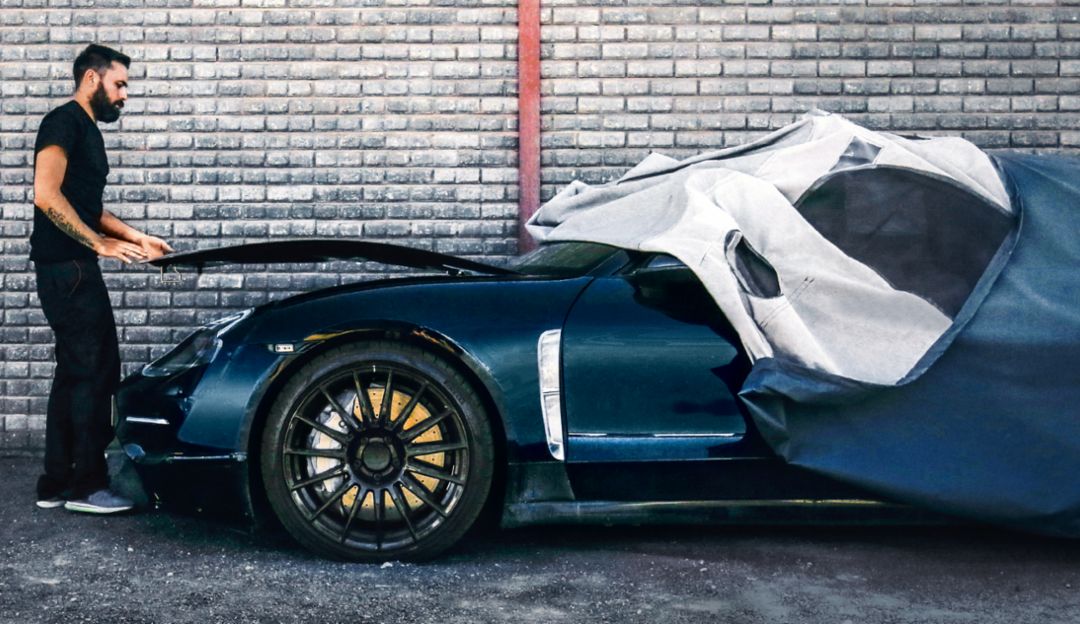